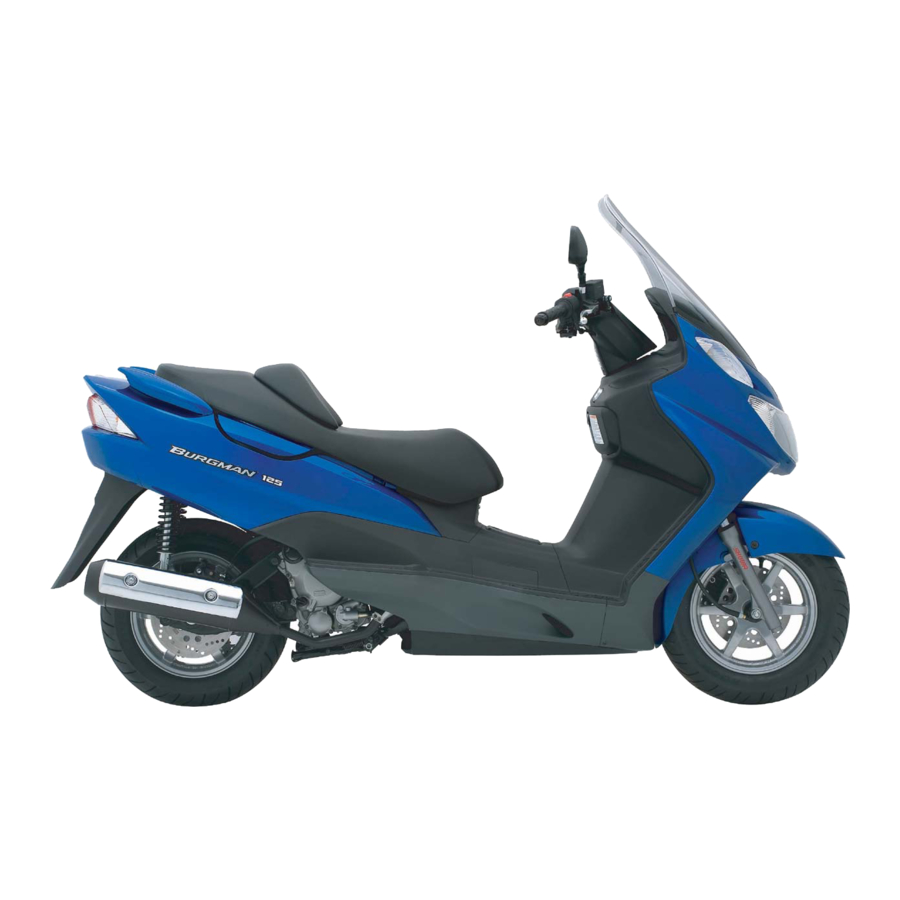
- Contents
- Table of Contents
- Troubleshooting
- Bookmarks
Related Manuals for Suzuki Burgman UH125
Summary of Contents for Suzuki Burgman UH125
- Page 1 UH125 9 9 5 0 0 - 3 1 3 5 0 - 0 1 E...
-
Page 2: Table Of Contents
FOREWORD GROUP INDEX This manual contains an introductory description on the SUZUKI UH125 and procedures for its inspec- tion/service and overhaul of its main components. GENERAL INFORMATION Other information considered as generally known is not included. Read the GENERAL INFORMATION section to... - Page 3 HOW TO USE THIS MANUAL TO LOCATE WHAT YOU ARE LOOKING FOR: 1. The text of this manual is divided into sections. 2. The section titles are listed in the GROUP INDEX. 3. Holding the manual as shown at the right will allow you to find the first page of the section easily.
- Page 4 Apply oil. Use engine oil unless other- Use engine coolant. wise specified. 99000-99032-11X Apply molybdenum oil solution. Use fork oil. (Mixture of engine oil and SUZUKI 99000-99044-10G MOLY PASTE in a ratio of 1:1) Apply SUZUKI SUPER GREASE "A" or equivalent. Apply or use brake fluid.
-
Page 5: Glossary
: Right Hand : Fuel Injection, Fuel Injector : Read Only Memory : Fuel Pump : Fuel Pressure Regulator : Society of Automotive Engineers : Suzuki Diagnosis System : Generator : Ground TO Sensor : Tip-Over Sensor (TOS) TP Sensor... - Page 6 WIRE COLOR : Black : Green :Pink : Blue : Gray : Red : Brown : Light blue : White : Dark green : Light green : Yellow : Dark gray : Orange B/Bl : Black with Blue tracer B/Br : Black with Brown tracer : Black with Green tracer B/Lg...
-
Page 7: General Information
GENERAL INFORMATION CONTENTS WARNING/CAUTION/NOTE................ 1- 2 GENERAL PRECAUTIONS ................. 1- 2 SUZUKI UH125K7 ('07-MODEL) ..............1- 4 SERIAL NUMBER LOCATION ..............1- 4 FUEL, OIL AND ENGINE COOLANT RECOMMENDATION ...... 1- 5 FUEL...................... 1- 5 ENGINE OIL AND FINAL GEAR OIL............ 1- 5 BRAKE FLUID.................. -
Page 8: Warning/Caution/Note
GENERAL INFORMATION WARNING/CAUTION/NOTE Please read this manual and follow its instructions carefully. To emphasize special information, the symbol and the words WARNING, CAUTION and NOTE have special meanings. Pay special attention to the mes- sages highlighted by these signal words. Indicates a potential hazard that could result in death or injury. - Page 9 GENERAL INFORMATION " * If parts replacement is necessary, replace the parts with Suzuki Genuine Parts or their equiva- lent. * When removing parts that are to be reused, keep them arranged in an orderly manner so that they may be reinstalled in the proper order and orientation.
-
Page 10: Suzuki Uh125K7 ('07-Model)
GENERAL INFORMATION SUZUKI UH125K7 ('07-MODEL) RIGHT SIDE LEFT SIDE • Difference between illustrations and actual motorcycle may exist depending on the markets. SERIAL NUMBER LOCATION The frame serial number or V.I.N. (Vehicle Identification Number) 1 is stamped on the right side of the frame. -
Page 11: Fuel, Oil And Engine Coolant Recommendation
Always select good quality engine oil. Use of SF/SG or SH/SJ in API classification with MA in JASO. Suzuki recommends the use of SAE 10W-40 engine oil. If SAE 10W-40 engine oil is not available, select an alternative accord- ing to the right chart. -
Page 12: Engine Coolant
Suzuki recommends the use of SUZUKI COOLANT anti-freeze/engine coolant. If this is not available, use an equivalent which is compatible with an aluminum radiator. -
Page 13: Break-In Procedures
GENERAL INFORMATION BREAK-IN PROCEDURES During manufacture only the best possible materials are used and all machined parts are finished to a very high standard but it is still necessary to allow the moving parts to "BREAK-IN" before subjecting the engine to maximum stresses. -
Page 14: Specifications
GENERAL INFORMATION SPECIFICATIONS DIMENSIONS AND DRY MASS Overall length................2 055 mm Overall width ................740 mm Overall height................1 240 mm Wheelbase ................1 465 mm Ground clearance ..............130 mm Seat height................735 mm Dry mass................. 148 kg ENGINE Type .................. -
Page 15: Electrical
GENERAL INFORMATION ELECTRICAL Ignition type................Electronic ignition (Transistorized) Ignition timing ................10° B.T.D.C. at 1 800 r/min Spark plug ................NGK CR8E or DENSO U24ESR-N Battery ..................12 V 28.8 kC (8 Ah)/10 HR Generator ................Three-phase A.C. generator Main fuse................. 30 A Fuse .................. -
Page 16: Periodic Maintenance
PERIODIC MAINTENANCE PERIODIC MAINTENANCE CONTENTS PERIODIC MAINTENANCE SCHEDULE ............ 2- 2 PERIODIC MAINTENANCE CHART............. 2- 2 LUBRICATION POINTS ................ 2- 3 MAINTENANCE AND TUNE-UP PROCEDURES ........2- 4 AIR CLEANER..................2- 4 COOLING FAN FILTER ................ 2- 5 EXHAUST PIPE NUTS AND MUFFLER BOLTS........2- 6 VALVE CLEARANCE................ -
Page 17: Periodic Maintenance Schedule
PERIODIC MAINTENANCE PERIODIC MAINTENANCE SCHEDULE The chart below lists the recommended intervals for all the required periodic service work necessary to keep the motorcycle operating at peak performance and economy. Mileages are expressed in terms of kilometer and time for your convenience. NOTE: More frequent servicing may be performed on motorcycles that are used under severe conditions. -
Page 18: Lubrication Points
PERIODIC MAINTENANCE LUBRICATION POINTS Proper lubrication is important for smooth operation and long life of each working part of the motorcycle. Major lubrication points are indicated below. Rear brake lever holder Speedometer gearbox Side-stand pivot and spring hooks Center stand pivot Speedometer and spring hooks cable... -
Page 19: Maintenance And Tune-Up Procedures
PERIODIC MAINTENANCE MAINTENANCE AND TUNE-UP PROCEDURES This section describes the servicing procedures for each item of the Periodic Maintenance requirements. AIR CLEANER (POLYURETHANE FOAM ELEMENT) Clean every 3 000 km (2 000 miles). (NON-WOVEN FABRIC ELEMENT) Inspect every 4 000 km (2 500 miles, 20 months) and replace every 12 000 km (7 000 miles). -
Page 20: Cooling Fan Filter
PERIODIC MAINTENANCE INSPECTION Non-woven fabric element • Inspect the element for clogging. If the element is clogged with dust, replace the element with a new one. Do not blow the element with compressed air. NOTE: If driving under dusty conditions, replace the air cleaner ele- ments more frequently. -
Page 21: Exhaust Pipe Nuts And Muffler Bolts
PERIODIC MAINTENANCE EXHAUST PIPE NUTS AND MUFFLER BOLTS Tighten initially at 1 000 km (600 miles, 3 months) and every 4 000 km (2 500 miles, 20 months) thereafter. • Remove the right side leg shield. ("8-8) • Remove the rear lower leg shield. ("8-8) •... -
Page 22: Spark Plug
PERIODIC MAINTENANCE NOTE: * The piston must be at "TDC" on the compression stroke in order to check the valve clearance or to adjust valve clear- ance. * The clearance specification is for COLD state. * To turn the crankshaft for clearance checking, and rotate in the normal running direction. -
Page 23: Fuel Line
PERIODIC MAINTENANCE SPARK PLUG GAP Measure the plug gap with the thickness gauge if it is correct. If not, adjust it to the following gap. $ Spark plug gap A: Standard: 0.7 – 0.8 mm % 09900-20803: Thickness gauge ELECTRODE'S CONDITION Inspect the worn or burnt condition of the electrodes. -
Page 24: Engine Oil And Oil Filter
PERIODIC MAINTENANCE ENGINE OIL AND OIL FILTER (ENGINE OIL) Replace Initially at 1 000 km (600 miles, 3 months) and every 4 000 km (2 500 miles, 20 months) thereafter. (OIL FILTER) Replace Initially at 1 000 km (600 miles, 3 months) and every 8 000 km (5 000 miles, 40 months) thereafter. -
Page 25: Final Gear Box Oil
2-10 PERIODIC MAINTENANCE • Replace the O-ring 3 with a new one. • Install new oil filter. • Install the spring 4 to the oil filter cap. • Replace the O-ring 5 with a new one. NOTE: Apply engine oil to the new O-ring 5. •... -
Page 26: Throttle Cable Play
PERIODIC MAINTENANCE 2-11 NOTE: If oil is dirty with sludge or used for a long period, drain the oil by removing the drain plug 3 and pour fresh oil through the oil level hole. # Oil drain plug: 12 N·m (1.2 kgf-m) $ Final gear box oil capacity Oil change : 150 ml Overhaul : 160 ml... -
Page 27: Cooling System
2-12 PERIODIC MAINTENANCE COOLING SYSTEM (RADIATOR HOSE) Inspect every 4 000 km (2 500 miles, 20 months). (ENGINE COOLANT) Replace engine coolant every 2 years. RADIATOR HOSE • Remove the rear lower leg shield. ("8-8) • Inspect the radiator hoses for crack, damage or engine cool- ant leakage. - Page 28 PERIODIC MAINTENANCE 2-13 ENGINE COOLANT CHANGE • Remove the rear lower leg shield. ("8-8) • Remove the radiator cap 1. • Drain engine coolant by disconnecting the radiator outlet hose & * Do not open the radiator cap when the engine is hot, as you may be injured by escaping hot liquid or vapor.
-
Page 29: Drive V-Belt
2-14 PERIODIC MAINTENANCE AIR BLEEDING FOR THE COOLING CIRCUIT • Add engine coolant up to the radiator inlet. • Slowly swing the motorcycle, right and left, to bleed the air trapped in the cooling circuit. • Add engine coolant up to the radiator inlet. •... -
Page 30: Brake System
PERIODIC MAINTENANCE 2-15 BRAKE SYSTEM (BRAKE) Inspect Initially at 1 000 km (600 miles, 3 months) and every 4 000 km (2 500 miles, 20 months) thereafter. (BRAKE HOSE AND BRAKE FLUID) Inspect Every 4 000 km (2 500 miles, 20 months). Replace hoses every 4 years. - Page 31 2-16 PERIODIC MAINTENANCE FRONT BRAKE PAD REPLACEMENT • Loosen the brake pad pin 1. • Remove the brake hose clamp bolt 2. • Remove the front brake caliper 3. • Remove the brake pads 4 by removing the brake pad bolt. •...
- Page 32 PERIODIC MAINTENANCE 2-17 FRONT BRAKE FLUID REPLACEMENT • Place the motorcycle on a level ground and keep the handle- bars straight. • Remove the front master cylinder reservoir cap and dia- phragm. • Suck up old brake fluid as much as possible. •...
- Page 33 2-18 PERIODIC MAINTENANCE AIR BLEEDING FOR THE FRONT BRAKE FLUID CIRCUIT Air trapped in the fluid circuit acts like a cushion to absorb a large proportion of the pressure developed by the master cylin- der and thus interferes with the full braking performance of the brake caliper.
-
Page 34: Tire
The standard tire fitted on this motorcycle is 110/90-13M/C 56P for front and 130/70-12 62P for rear. The use of tires other than those specified may cause instability. It is highly recommended to use a SUZUKI Genuine Tire. $ TIRE TYPE... -
Page 35: Steering
2-20 PERIODIC MAINTENANCE STEERING Inspect initially at 1 000 km (600 miles, 3 months) and every 8 000 km (5 000 miles, 40 months) thereafter. Steering should be adjusted properly for smooth turning of han- dlebars and safe running. Overtight steering prevents smooth turning of the handlebars and too loose steering will cause poor stability. -
Page 36: Chassis Bolt And Nut
PERIODIC MAINTENANCE 2-21 CHASSIS BOLT AND NUT Tighten initially at 1 000 km (600 miles, 3 months) and every 4 000 km (2 500 miles, 20 months) thereafter. Check that all chassis bolts and nuts are tightened to their specified torque. (Refer to pages 2-20 and 21 for the locations of the following nuts and bolts on the motorcycle.) Item N·m... - Page 37 2-22 PERIODIC MAINTENANCE...
-
Page 38: Compression Pressure Check
PERIODIC MAINTENANCE 2-23 COMPRESSION PRESSURE CHECK The compression of a cylinder is a good indicator of its internal condition. The decision to overhaul the cylinder is often based on the results of a compression test. Periodic maintenance records kept at your dealership should include compression readings for each maintenance service. -
Page 39: Oil Pressure Check
2-24 PERIODIC MAINTENANCE OIL PRESSURE CHECK Check the oil pressure periodically. This will give a good indication of the condition of the moving parts. OIL PRESSURE SPECIFICATION Above 170 kPa (1.7 kgf/cm at 3 000 r/min., Oil temp. at 60 °C Below 230 kPa (2.3 kgf/cm If the oil pressure is lower or higher than the specification, the following causes may be considered. -
Page 40: Automatic Clutch Inspection
PERIODIC MAINTENANCE 2-25 AUTOMATIC CLUTCH INSPECTION This motorcycle is equipped with an automatic clutch and vari- able ratio belt drive transmission. The engagement of the clutch is governed by engine RPMs and centrifugal mechanism located in the clutch. To insure proper performance and longer lifetime of the clutch assembly it is essential that the clutch engages smoothly and gradually. -
Page 41: Sds Check
2-26 PERIODIC MAINTENANCE SDS CHECK Using SDS, sample the data at the time of new and periodic vehicle inspections. After saving the sampled data in the computer, file them by model and by user. The periodically filed data help improve the accuracy of troubleshooting since they can indicate the condition of vehicle functions that has changed with time. - Page 42 PERIODIC MAINTENANCE 2-27 Data at 3 000 r/min under no load Approx. 3 000 r/min Check the engine coolant temperature. XX ˚C ˚ Check the manifold absolute pressure. XX kPa Data at the time of racing ˚ Check the manifold absolute pressure in according with the throttle valve opening.
- Page 43 2-28 PERIODIC MAINTENANCE Data of intake negative pressure during idling (100 °C) ˚ Check the engine coolant temperature. Approx. 100 ˚C Check the manifold absolute pressure. XX kPa Data of manifold absolute pressure operation at the time of starting Check the manifold absolute pressure. XX kPa...
- Page 44 PERIODIC MAINTENANCE 2-29 Example of trouble Three data; value 1 (current data 1), value 2 (past data 2) and value 3 (past data 3); can be made in compar- ison by showing them in the graph. Read the change of value by comparing the current data to the past data that have been saved under the same condition, then you may determine how changes have occurred with the pass of time and identify what problem is currently occurring.
- Page 45 ENGINE ENGINE CONTENTS ENGINE COMPONENTS REMOVABLE WITH THE ENGINE IN PLACE .. 3- 2 ENGINE REMOVAL AND REMOUNTING........... 3- 3 REMOVAL ..................... 3- 3 REMOUNTING ..................3- 7 ENGINE DISASSEMBLY ................3-10 ENGINE COMPONENT INSPECTION AND SERVICE ....... 3-20 ROCKER ARM AND SHAFT ..............3-20 CYLINDER HEAD ..................
-
Page 46: Engine Components Removable With The Engine In Place
ENGINE ENGINE COMPONENTS REMOVABLE WITH THE ENGINE IN PLACE The parts listed below can be removed and reinstalled without removing the engine from the frame. Refer to page listed in each section for removal and reinstallation instructions. ENGINE CENTER ITEM REMOVAL INSPECTION INSTALLATION... -
Page 47: Engine Removal And Remounting
ENGINE ENGINE REMOVAL AND REMOUNTING REMOVAL • Remove the trunk box. (!8-11) • Remove the rear lower leg shield. (!8-8) • Drain engine oil. (!2-9) • Drain engine coolant. (!2-12) • Drain final gear box oil. (!2-10) • Disconnect the battery - lead wire. •... - Page 48 ENGINE • Disconnect the radiator inlet hose 5. • Disconnect the engine coolant temperature meter lead wire 6, ignition coil lead wires 7 and ECT sensor coupler 8. • Disconnect the TP sensor coupler 9, IAP sensor coupler 0, ISC valve coupler A and injector coupler B. •...
- Page 49 ENGINE • Loosen the muffler connecting bolt I. • Remove the muffler. • Remove the exhaust pipe J. • Disconnect the radiator outlet hose K. • Remove the exhaust pipe gasket L. • Remove the rear brake caliper M. • Remove the rear axle nut N and collar. •...
- Page 50 ENGINE • Support the engine using a jack. • Remove the rear shock absorber mounting bolt (LH). • Remove the engine mounting bolt/nut. • Remove the engine from the frame. • Remove the crankcase bracket Q.
-
Page 51: Remounting
ENGINE REMOUNTING Remount the engine in the reverse order of removal. Pay atten- tion to the following points: • Install the crankcase bracket A to the engine, and insert the crankcase bracket bolt B from the left side. • Position the crankcase bracket correctly by inserting a steel plate C of 2.5 mm thickness. - Page 52 ENGINE • Tighten the engine mounting nut E and rear shock absorber mounting bolt D to the specified torque. " Engine mounting nut: 100 N·m (10.0 kgf-m) Lower rear shock absorber mounting bolt: 29 N·m (2.9 kgf-m) • Install the rear wheel and rear swingarm 1. "...
- Page 53 ENGINE • Install the insulator and throttle body assembly. $ 09930-11910: Torx wrench NOTE: * Face the O-ring side of insulator to the engine. * Face the tab F of insulator to forward. * Use new twist-off bolts. CAUTIONS AFTER REINSTALLATON •...
-
Page 54: Engine Disassembly
3-10 ENGINE ENGINE DISASSEMBLY Identify the position of each removed part. Organize the parts in their respective groups (e.g., intake, exhaust) so that they can be reinstalled in their origi- nal positions. IGNITION COIL AND SPARK PLUG • Remove the ignition coil 1. •... - Page 55 ENGINE 3-11 CAMSHAFT • Remove the generator cover plug 1. • Bring the piston to TDC on the compression stroke by turning the crankshaft until the line A on the generator rotor aligns with the mark B on the generator cover. •...
- Page 56 3-12 ENGINE • Slide and drop the camshaft sprocket to the camshaft groove • Disengage the cam chain from the camshaft sprocket. • Remove the camshaft journal holder No.1 5. • Remove the camshaft 6 and camshaft sprocket. • Remove the dowel pins and C-ring 7. CYLINDER HEAD •...
- Page 57 ENGINE 3-13 • Remove the cylinder head gasket 1 and dowel pins. CYLINDER • Remove the cam chain guide 1. • Remove the cylinder nuts. • Remove the cylinder. • Remove the cylinder gasket 2 and dowel pins. PISTON • Remove the piston pin circlip 1. •...
- Page 58 3-14 ENGINE OIL FILTER • Remove the oil filter cap 1. • Remove the oil filter 2. • Remove the O-ring 3. WATER PUMP • Remove the water pump assembly 1. GENERATOR COVER • Remove the generator cover 1. • Remove the gasket 2 and dowel pins.
- Page 59 ENGINE 3-15 GENERATOR ROTOR AND STARTER DRIVEN GEAR • Remove the starter idle gear shaft 1 and starter idle gear 2. • With the generator rotor held immovable with the special tool, remove the generator rotor nut. $ 09930-44520: Rotor holder •...
- Page 60 3-16 ENGINE • Remove the oil pump driven sprocket and oil pump 2 along with the oil pump drive chain 3. • Remove the cam chain 4. CRANKSHAFT RIGHT BEARING NUT • Insert a proper steel rod into the crankcase hole A and pass it through the crankshaft web holes in order to prevent the crankshaft from turning.
- Page 61 ENGINE 3-17 • With the fixed drive face 2 held immovable using the special tool, loosen the nut. • Remove the washer. • Remove the fixed drive face. $ 09930-40113: Rotor holder • With the clutch housing 3 held immovable using the special tool, remove the nut.
- Page 62 3-18 ENGINE • Remove the dowel pins. • Remove the idle gear 2. • Remove the shim 3. • Remove the final driven gear/rear axle shaft 4. • Remove the driveshaft 5 by tapping it with a plastic mallet. OIL SUMP FILTER •...
- Page 63 ENGINE 3-19 CRANKCASE • Remove the 6 mm crankcase bolts first, then 8 mm ones evenly and diagonally. CRANKSHAFT • Separate the crankcase into left and right halves using the special tool. $ 09920-13120: Crankcase/crankshaft separator NOTE: * Set the special tool so that the tool arms are in parallel with the end face of crankcase.
-
Page 64: Engine Component Inspection And Service
3-20 ENGINE ENGINE COMPONENT INSPECTION AND SERVICE ROCKER ARM AND SHAFT DISASSEMBLY • Pull out the rocker arm shafts 1. • Remove the intake 2 and exhaust 3 valve rocker arms and wave washers 4. ROCKER ARM SHAFT OUTSIDE DIAMETER INSPECTION •... -
Page 65: Cylinder Head
ENGINE 3-21 CYLINDER HEAD DISASSEMBLY • Remove the cam chain tensioner 1. • Remove the thermostat cover 2. • Remove the thermostat 3. • Compress the valve spring using the special tools. • Remove the cotter halves 4. $ 09916-14510: Valve lifter 09916-14910: Attachment 09916-84511: Tweezers •... -
Page 66: Cylinder Head Distortion
3-22 ENGINE • Remove the oil seal 8 and spring seat 9. Do not reuse the removed oil seal. • Remove the other valves in the same manner as described previously. CYLINDER HEAD DISTORTION • Decarbonize the combustion chambers. • Check the gasket surface of the cylinder head for distortion with a straightedge and thickness gauge, taking a clearance reading at several places indicated. - Page 67 ENGINE 3-23 VALVE HEAD RADIAL RUNOUT • Place the dial gauge at a right angle to the valve head face and measure the valve head radial runout. • If it measures more than the service limit, replace the valve. % Valve head radial runout: Service Limit: 0.03 mm $ 09900-20607: Dial gauge (1/100 mm) 09900-20701: Magnetic stand...
- Page 68 3-24 ENGINE VALVE GUIDE SERVICING • Using the valve guide remover 1, drive the valve guide out toward the camshaft side. $ 09916-44310: Valve guide remover/installer NOTE: * Discard the removed valve guide subassemblies. * Only oversized valve guides are available as replacement parts.
- Page 69 ENGINE 3-25 • After installing the valve guide, re-finish the guiding bore using the reamer 7. • Clean and oil the guides after reaming. $ 09916-34570: Valve guide reamer 09916-34542: Reamer handle NOTE: * Be sure to cool down the cylinder head to ambient air temper- ature.
- Page 70 3-26 ENGINE VALVE SEAT SERVICING • The valve seats 1 for both the intake valves and exhaust valves are machined to four different angles. The seat contact surface is cut at 45°. INTAKE EXHAUST Valve seat angles 30°, 45°, 60° 15°, 45°...
- Page 71 ENGINE 3-27 VALVE SPRING The force of the coil spring keeps the valve seat tight. Weak- ened spring result in reduced engine power output, and often account for the chattering noise coming from the valve mecha- nism. • Check the valve spring for proper strength by measuring its free length and also by the force required to compress it.
-
Page 72: Camshaft
3-28 ENGINE • Compress the valve spring using the special tools. $ 09916-14510: Valve lifter 09916-14910: Attachment 09916-84511: Tweezers Compressing of the valve spring must be limited to the extent only necessary to prevent the spring from fatigue. • Install the valve cotter halves 2. Check that the rounded lip E of the cotter is securely fitted in the groove F in the valve stem end. - Page 73 ENGINE 3-29 • Tighten the camshaft journal holder bolts evenly and diago- nally to the specified torque. " Camshaft journal holder bolt: 10 N·m (1.0 kgf-m) NOTE: Do not rotate the camshaft with the plastigauge in place. • Remove the camshaft holder, and read the width of the com- pressed plastigauge with envelope scale.
-
Page 74: Cam Chain Tension Adjuster
3-30 ENGINE CAM CHAIN TENSION ADJUSTER CAM CHAIN TENSION ADJUSTER INSPECTION • Check that the push rod 1 can slide smoothly with the lock 2 of the ratchet mechanism released. If it does not slide smoothly or the ratchet mechanism is worn or damaged, replace the cam chain tension adjuster with a new one. -
Page 75: Cylinder
ENGINE 3-31 CYLINDER CYLINDER DISTORTION • Check the gasket surface of the cylinder for distortion with a straightedge and thickness gauge, taking a clearance reading at several places as indicated. • If the largest reading at any position of the straightedge exceeds the limit, replace the cylinder with a new one. - Page 76 3-32 ENGINE PISTON PIN AND PIN BORE • Measure the piston pin bore diameter using the small bore gauge. • If the measurement is out of specification, replace the piston. % Piston pin bore I.D.: Service Limit: 16.030 mm $ 09900-20602: Dial gauge (1/1 000 mm) 09900-22401: Small bore gauge (10 –...
-
Page 77: Conrod And Crankshaft
ENGINE 3-33 PISTON RING FREE END GAP AND PISTON RING END GAP • Measure the piston ring free end gap using the vernier cali- pers. • Next, fit the piston ring squarely into the cylinder and measure the piston ring end gap using the thickness gauge. •... - Page 78 3-34 ENGINE CONROD DEFLECTION INSPECTION • Move the small end sideways while holding the big end immovable in thrust direction. • Measure the amount of deflection. • Turn the conrod and see if it moves smoothly without play and noise. •...
-
Page 79: Oil Pump
ENGINE 3-35 OIL PUMP INSPECTION • Rotate the oil pump by hand and check that it moves smoothly. • If it does not move smoothly, replace the oil pump assembly with a new one. DISASSEMBLY • Remove the circlip 1. •... -
Page 80: Movable Drive Face Assembly
3-36 ENGINE MOVABLE DRIVE FACE ASSEMBLY DISASSEMBLY • Remove the spacer 1. • Remove the movable drive face cover 2. • Remove the movable drive plate 3. • Remove the dampers 4. • Remove the rollers 5. INSPECTION Movable face •... - Page 81 ENGINE 3-37 Spacer • Inspect the spacer for any wear or damage. If any defects are found, replace the spacer with a new one. Roller • Inspect the rollers for abnormal wear or other damage. If any defects are found, replace the rollers as a set. REASSEMBLY Assemble the movable drive face in the reverse order of disas- sembly.
-
Page 82: Clutch Shoe/Movable Driven Face
3-38 ENGINE CLUTCH SHOE/MOVABLE DRIVEN FACE DISASSEMBLY • Attach the special tool to the clutch shoe/movable driven face assembly and compress the assembly by turning in the spe- cial tool handle. • Remove the clutch shoe nut 1. $ 09922-31420: Clutch spring compressor Since a high spring force applies to the clutch shoe/movable driven face assembly, care must be used so as not to cause the clutch shoe and movable... - Page 83 ENGINE 3-39 • Remove the rollers 5 from the pins. • Remove the movable driven face 6 from the fixed driven face • Remove the O-rings 8 and oil seal 9. • Remove the oil seal 0. • Remove the needle bearing using the special tool. $ 09921-20240: Bearing remover set (20 mm) NOTE: If abnormal noise does not occur, it is not necessary to remove...
- Page 84 3-40 ENGINE • Remove the snap ring A. • Remove the bearing using the special tool. $ 09913-70210: Bearing installer set (22 mm) NOTE: If abnormal noise does not occur, it is not necessary to remove the bearing. INSPECTION Clutch shoe •...
- Page 85 ENGINE 3-41 Movable driven face spring • Measure the spring free length A using the vernier calipers. • If the length is shorter than the service limit, replace the spring with a new one. % Movable driven face spring free length: Service Limit: 123.5 mm $ 09900-20102: Vernier calipers Drive V-belt...
- Page 86 • Install needle bearing 3 using an appropriate specer. Use a new bearing. • Apply grease to both bearings. Fill sufficient grease in the grease groove inside the fixed driven face and also on the bearings. ) 99000-25010: SUZUKI SUPER GREASE "A" or equivalent...
- Page 87 $ 09913-70210: Bearing installer set Use new oil seals and O-rings. • Apply grease both to the lip of oil seals and O-rings. ) 99000-25010: SUZUKI SUPER GREASE "A" or equivalent • Apply grease to the grease groove and sliding surface of mov- able driven face 6.
-
Page 88: Starter Clutch
3-44 ENGINE • Install the movable driven face seat 8. Align the hole on the seat with the hole on the mov- able driven face. • Set the spring and clutch shoe to the movable driven face. Engage each end of the spring with the respective holes, one provided on the movable driven face and the other on the clrtch shoe plate. - Page 89 ENGINE 3-45 • Inspect the starter driven gear bushing for any damages. DISASSEMBLY • Remove the starter clutch 1 and shim 2. $ 09930-44520: Rotor holder • Remove the rollers 3, push pieces 4 and springs 5. REASSEMBLY Reassemble the starter clutch in the reverse order of removal. Pay attention to the following points: •...
-
Page 90: Generator Cover
3-46 ENGINE GENERATOR COVER DISASSEMBLY • Remove the generator stator 1 and CKP sensor 2. • Remove the snap ring 3. • Remove the bearing using the special tool. $ 09921-20240: Bearing remover set (12 mm) • Remove the oil seal 4. - Page 91 ENGINE 3-47 REASSEMBLY Reassemble the generator cover in the reverse order of disas- sembly. Pay attention to the following points: • Install oil seal using the special tool. $ 09913-70210: Bearing installer set (22 mm) * Use a new oil seal. * Install the oil seal with the marked code toward out- side.
-
Page 92: Final Gear Box Cover
3-48 ENGINE FINAL GEAR BOX COVER DISASSEMBLY • Remove the O-ring 1. • Remove the bearing retainer 2. • Remove the bearing 3 using the special tool. $ 09921-20240: Bearing remover set NOTE: If abnormal noise does not occur, it is not necessary to remove the bearing. - Page 93 • Install the oil seal. $ 09913-70210: Bearing installer set • Apply grease to the lip of oil seal. ) 99000-25010: SUZUKI SUPER GREASE "A" or equivalent • Install the bearing 3 using the special tool. $ 09913-70210: Bearing installer set (47 mm) •...
-
Page 94: Final Gear
3-50 ENGINE FINAL GEAR INSPECTION Inspect the removed gears and shafts for the following abnor- malities. * Drive gear, idle gear and driven gear damage or wear * Improper tooth contact * Shaft spline damage CRANKCASE Play BEARING INSPECTION Play Rotate the bearing inner race by finger to inspect for abnormal play, noise and smooth rotation while the bearings are in the crankcase. - Page 95 ENGINE 3-51 • Remove the oil seal 3. $ 09913-50121: Oil seal remover The removed oil seal should be replaced with a new one. • Remove the bearings (4, 5, 6) using the special tools. $ 09913-70210: Bearing installer set (35 mm) 09921-20240: Bearing remover set (15 mm) 09921-20240: Bearing remover set (17 mm) NOTE:...
- Page 96 • Install new oil seal 2 using the special tool. $ 09913-70210: Bearing installer set (72 × 75 mm) • Apply grease to the lip of oil seal. ) 99000-25010: SUZUKI SUPER GREASE "A" or equivalent • Install the bearing 3 using the special tool.
- Page 97 ENGINE 3-53 • Apply THREAD LOCK SUPER to the bolts. • Install the plate 7. * 99000-32110: THREAD LOCK SUPER "1322" or equivalent BEARING REMOVAL (RIGHT CRANKCASE) • Remove the bearing using the special tool. $ 09913-70210: Bearing installer set (42 × 47 mm) NOTE: If abnormal noise does not occur, it is not necessary to remove the bearing.
- Page 98 3-54 ENGINE OIL NOZZLE INSTALLATION • Fit new O-ring to the oil nozzle. • Apply THREAD LOCK to the bolt, tighten it securely. + 99000-32050: THREAD LOCK "1342" or equivalent NOTE: Before installing the oil nozzle, clean its oil passage. BUSHING INSPECTION Inspect the engine mounting bushings 1, 2 and rear suspen- sion bushing 3 for wear or damage.
- Page 99 ENGINE 3-55 ENGINE MOUNTING BUSHING INSTALLATION • Using an appropriate side steel tube and vise, press in the bushing 1 into the crankcase 2. * Knurling side of the bushings must face inside. * Align the bushing end A with the crankcase surface. REAR SHOCK ABSORBER BUSHING Remove and install the rear shock absorber bushing in the same manner of engine mounting bushing removal and installation.
-
Page 100: Engine Reassembly
3-56 ENGINE ENGINE REASSEMBLY Reassembly is in the reverse order of removal. Pay attention to the following points: * Make sure to coat the rotating and sliding sections with engine oil. * Care must be taken so that the drive V-belt, drive face and driven face are completely free from oil and grease. - Page 101 • Clean and degrease the crankcase mating surfaces (both sur- faces). • Fit the dowel pins 1 into the left crankcase. • Apply SUZUKI BOND to the both crankcases. , 99000-31110: SUZUKI BOND "1215" or equivalent * Coat the sealant evenly without break.
- Page 102 3-58 ENGINE • Fit the radiator hose guide 2. • Tighten the 8 mm crankcase bolts first, then 6 mm ones evenly and diagonally. " Crankcase bolt 8 mm: 22 N·m (2.2 kgf-m) Crankcase bolt 6 mm: 11 N·m (1.1 kgf-m) NOTE: After crankcase bolts have been tightened, make sure that the crankshaft rotates smoothly.
- Page 103 ENGINE 3-59 IDLE SHAFT SHIM SELECTION In order to obtain proper clearance for the idle shaft, 7 kinds of shims in different thickness are available. Inspect the clearance as follows and replace the shim if neces- sary. • Degreace the idle shaft and shim 1. •...
- Page 104 3-60 ENGINE • If the measured clearance is not within the specification, mea- sure the thickness of the shim 1 with the micrometer and select the specified shim from the table below. $ 09900-20205: Micrometer (0 – 25 mm) % Idle shaft shim selection table PART NO.
- Page 105 ENGINE 3-61 • Check that no roller inside the movable drive face is out of the slot. • Install the movable drive face 3. * The assembly work should be carefully performed so as not to allow the roller to dislocate. * Check that the movable drive face is properly engaged with the spline.
- Page 106 3-62 ENGINE • To obtain proper contact of the drive V-belt, turn the fixed drive face until the fixed drive face and the movable driven face can rotate synchronously. • Fit a new clutch cover gasket. • Install the clutch cover 8. Bolts must be tightened diagonally and evenly.
- Page 107 ENGINE 3-63 OIL PUMP • Engage the oil pump drive chain 1 with the oil pump gear. • Install the oil pump and cover. GENERATOR ROTOR AND STARTER DRIVEN GEAR • Install the key 1. • Install the generator rotor 2 together with the starter driven gear 3.
- Page 108 Use the new O-rings to prevent engine coolant leakage. • Apply engine coolant to the O-ring 1. • Apply grease to the O-ring 2. ) 99000-25010: SUZUKI SUPER GREASE "A" or equivalent • Install the water pump assembly 3. Align the boss A of the water pump shaft end with the...
- Page 109 ENGINE 3-65 • Fit the clamp C in position. • Tighten the water pump bolts. OIL FILTER • Install the O-ring 1. • Install the oil filter 2. • Install the O-ring 3 and spring 4. * Use new O-rings to prevent the engine oil leakage. * Position the oil filter so that the valve A faces out- side.
- Page 110 3-66 ENGINE • Install the 2nd ring 3 and 1st ring 4. NOTE: 2nd ring 3 and 1st ring 4 differ in shape. • Face the stamped mark A upward when assembling. 1st ring 2nd ring • After installing all the piston rings, check that each ring rotates smoothly.
- Page 111 ENGINE 3-67 CYLINDER • Install the dowel pins and a new gasket 1 to the crankcase. Replace the gasket with a new one. • Coat the cylinder wall and piston surface with engine oil. • Install the cylinder. When inserting the piston into the cylinder, take care not to bend the piston ring.
- Page 112 3-68 ENGINE NOTE: * The rounded side of the washer 2 should be positioned upside. * Apply engine oil to the washers 2 and thread of the bolts before installing them. • Tighten the cylinder base nuts and cylinder head nuts to the specified torque.
- Page 113 ENGINE 3-69 • Install the camshaft 2 and camshaft sprocket 3. Position the camshaft sprocket so that the stamped mark side faces outside. • Align the engraved lines C on the camshaft end with the cyl- inder head top surface. •...
- Page 114 3-70 ENGINE • Install the dowel pins. • Install the camshaft holder No.2 5 and tighten the bolts to the specified torque. " Camshaft holder bolt: 10 N·m (1.0 kgf-m) When installing the camshaft holder No.2, the pro- truded side must be face outside. CAM CHAIN TENSION ADJUSTER •...
- Page 115 • Install the gasket to the cylinder head cover. Replace the gasket with a new one. • Apply SUZUKI BOND to the points shown in the photo. . 99000-31160: SUZUKI BOND "1207B" or equivalent • Install the cylinder head cover.
-
Page 116: Fi System Diagnosis
FI SYSTEM DIAGNOSIS FI SYSTEM DIAGNOSIS CONTENTS PRECAUTIONS IN SERVICING ..............4- 3 ELECTRICAL PARTS ................4- 3 FUSE...................... 4- 4 SWITCH ....................4- 4 ECM/VARIOUS SENSORS ..............4- 4 ELECTRICAL CIRCUIT INSPECTION PROCEDURE......4- 6 USING THE MULTI-CIRCUIT TESTER..........4- 9 FI SYSTEM TECHNICAL FEATURES............ - Page 117 FI SYSTEM DIAGNOSIS FI SYSTEM DIAGNOSIS CONTENTS "23" (P1651-H/L) TO SENSOR CIRCUIT MALFUNCTION....4-47 "24" (P0351) IGNITION SYSTEM MALFUNCTION......4-50 "32" (P0201) FUEL INJECTOR CIRCUIT MALFUNCTION ....4-51 "40" (P0505 or P0506 and P0507) ISC VALVE CIRCUIT MALFUNCTION..................4-53 "41" (P0230-H/L) FP CIRCUIT MALFUNCTION ........4-57 "42"...
-
Page 118: Precautions In Servicing
FI SYSTEM DIAGNOSIS PRECAUTIONS IN SERVICING When handling the component parts or servicing the FI system, observe the following points for the safety of the system. ELECTRICAL PARTS CONNECTOR/COUPLER • When connecting a connector, be sure to push it in until a click is felt. -
Page 119: Fuse
FI SYSTEM DIAGNOSIS • When connecting meter probe from the terminal side of the coupler (where connection from harness side not being possi- ble), use extra care not to force and cause the male terminal to bend or the female terminal to open. Connect the probe as shown to avoid opening of female ter- minal. - Page 120 FI SYSTEM DIAGNOSIS • When disconnecting and connecting the ECM, make sure to turn OFF the ignition switch 1, or electronic parts may get damaged. INCORRECT • Battery connection in reverse polarity is strictly prohibited. Such a wrong connection will damage the components of the FI system instantly when reverse power is applied.
-
Page 121: Electrical Circuit Inspection Procedure
FI SYSTEM DIAGNOSIS ELECTRICAL CIRCUIT INSPECTION PROCEDURE While there are various methods for electrical circuit inspection, described here is a general method to check for open and short circuit using an ohmmeter and a voltmeter. OPEN CIRCUIT CHECK Possible causes for the open circuits are as follows. As the cause can exist in the connector/coupler or terminal, they need to be checked carefully. - Page 122 FI SYSTEM DIAGNOSIS Continuity check • Measure resistance across coupler B (between A and C in the figure). If no continuity is indicated (infinity or over limit), the circuit is open between terminals A and C. 1 ECM • Disconnect the coupler B and measure resistance between couplers A and B.
- Page 123 FI SYSTEM DIAGNOSIS SHORT CIRCUIT CHECK (WIRE HARNESS TO GROUND) • Disconnect the negative cable from the battery. • Disconnect the connectors/couplers at both ends of the circuit to be checked. NOTE: If the circuit to be checked branches to other parts as shown, disconnect all connectors/couplers of those parts.
-
Page 124: Using The Multi-Circuit Tester
FI SYSTEM DIAGNOSIS USING THE MULTI-CIRCUIT TESTER • Use the Suzuki multi-circuit tester set (09900-25008). • Use well-charged batteries in the tester. • Be sure to set the tester to the correct testing range. USING THE TESTER • Incorrectly connecting the + and - probes may cause the inside of the tester to burnout. -
Page 125: Fi System Technical Features
4-10 FI SYSTEM DIAGNOSIS FI SYSTEM TECHNICAL FEATURES INJECTION TIME (INJECTION VOLUME) The factors to determine the injection time include the basic fuel injection time, which is calculated on the basis of intake air pressure, engine speed and throttle opening angle, and various compensations. These compensations are determined according to the signals from various sensors that detect the engine and driving conditions. -
Page 126: Compensation Of Injection Time (Volume)
FI SYSTEM DIAGNOSIS 4-11 COMPENSATION OF INJECTION TIME (VOLUME) The following different signals are output from the respective sensors for compensation of the fuel injection time (volume). SIGNAL DESCRIPTION ENGINE COOLANT TEMPERATURE SEN- When engine coolant temperature is low, injection time (vol- SOR SIGNAL ume) is increased. -
Page 127: Fi System Parts Location
4-12 FI SYSTEM DIAGNOSIS FI SYSTEM PARTS LOCATION A ECM D Crankshaft Position Sensor (CKPS) B Fuel Injector E Heated Oxygen Sensor (HO2S) C Intake Air Pressure Sensor (IAPS) F Fuel Pump (FP) - Page 128 FI SYSTEM DIAGNOSIS 4-13 A ECM J Throttle Position Sensor (TPS) G Speedometer K Engine Coolant Temperature Sensor (ECTS) H Tip-Over Sensor (TOS) L Ignition coil (IG coil) I Idle Speed Control valve (ISC valve)
-
Page 129: Fi System Wiring Diagram
4-14 FI SYSTEM DIAGNOSIS FI SYSTEM WIRING DIAGRAM... -
Page 130: Ecm Terminal
FI SYSTEM DIAGNOSIS 4-15 ECM TERMINAL ECM coupler TERMINAL TERMINAL CIRCUIT CIRCUIT Starter motor Mode select switch Mode select switch HO2 sensor (OX) TO sensor (TO) ECT sensor (ECT) — Ignition switch — IAP sensor (IAP) CKP sensor (CKP+) TP sensor (TP) ECM ground (E1) Sensor ground (E2) ISC valve motor (IS2B) -
Page 131: Self-Diagnosis Function
4-16 FI SYSTEM DIAGNOSIS SELF-DIAGNOSIS FUNCTION The self-diagnosis function is incorporated in the ECM. The function has two modes, "User mode" and "Dealer mode". The user can only be notified by the FI indicator light. To check the function of the individual FI system devices, the dealer mode is provided. -
Page 132: Dealer Mode
FI SYSTEM DIAGNOSIS 4-17 DEALER MODE The defective function is memorized in the ECM. Use the special tool's coupler to connect to the dealer mode coupler. The memorized malfunction code is displayed by the flashing pattern of FI indicator light. Malfunction means that the ECM does not receive signal from the devices. -
Page 133: Fail-Safe Function
4-18 FI SYSTEM DIAGNOSIS CODE MALFUNCTION PART REMARKS None No defective part Crankshaft position sensor (CKPS) Pick-up coil signal Intake air pressure sensor (IAPS) Throttle position sensor (TPS) Engine coolant temperature sensor (ECTS) Tip-over sensor (TOS) Ignition signal (IG coil) Injector signal (FI) ISC valve Fuel pump control system (FP control system) -
Page 134: Fi System Troubleshooting
FI SYSTEM DIAGNOSIS 4-19 FI SYSTEM TROUBLESHOOTING CUSTOMER COMPLAINT ANALYSIS Record details of the problem (failure, complaint) and how it occurred as described by the customer. For this purpose, use of such an inspection form such as below will facilitate collecting information required for proper analysis and diagnosis. -
Page 135: Visual Inspection
4-20 FI SYSTEM DIAGNOSIS MOTORCYCLE/ENVIRONMENTAL CONDITION WHEN PROBLEM OCCURS Environmental condition Weather Fair Cloudy Rain Snow Always Other Temperature Warm Cool Cold ( °C) Always Frequency Always Sometimes ( times/ day, month) Only once Under certain condition Road Urban Suburb Highway Mountainous ( Uphill... -
Page 136: Self-Diagnostic Procedures
FI SYSTEM DIAGNOSIS 4-21 SELF-DIAGNOSTIC PROCEDURES NOTE: * Do not disconnect the coupler from ECM, battery cable from battery, ECM ground wire from engine or main fuse before confirming the DTC (Diagnostic Trouble Code) stored in mem- ory. Such disconnection will erase the memorized information in ECM memory. -
Page 137: Understanding The Dtc (Diagnostic Trouble Code)
4-22 FI SYSTEM DIAGNOSIS UNDERSTANDING THE DTC (Diagnostic Trouble Code) A two-digit DTC is shown through the flashing pattern of the FI indicator light. The DTCs are displayed from a smaller number to a larger number in that order. When all the applicable DTCs have been displayed, the displaying of the DTCs repeat from the first one again. -
Page 138: Dtc Indication Chart
FI SYSTEM DIAGNOSIS 4-23 DTC INDICATION CHART FLASHING PATTERN DTC No. MALFUNCTION PART None CKP sensor (#4-30) IAP sensor (#4-33) TP sensor (#4-38) ECT sensor (#4-43) TO sensor (#4-47) Ignition coil (#4-50) Fuel injector (#4-51) ISC valve (#4-53) Fuel pump (#4-57) Ignition switch (#4-59) HO2 sensor (#4-60) -
Page 139: Self-Diagnosis Reset Procedure
4-24 FI SYSTEM DIAGNOSIS 40 code has no first digit display. For this reason, the interval A between the displays as shown below is longer than the others. 4.0 sec. 1.0 sec. SELF-DIAGNOSIS RESET PROCEDURE • After repairing the trouble, turn OFF the ignition switch and turn ON again. -
Page 140: Use Of Sds Diagnostic Procedures
FI SYSTEM DIAGNOSIS 4-25 USE OF SDS DIAGNOSTIC PROCEDURES * Do not disconnect the coupler from ECM, battery cable from battery, ECM ground wire from engine or main fuse before confirming the DTC (Diagnostic Trouble Code) stored in mem- ory. Such disconnection will erase the memorized information in ECM memory. -
Page 141: Use Of Sds Diagnosis Reset Procedure
4-26 FI SYSTEM DIAGNOSIS USE OF SDS DIAGNOSIS RESET PROCEDURE • After repairing the trouble, turn OFF the ignition switch and turn ON again. • Click the DTC inspection button 1. • Check the DTC. • The previous malfunction history code (Past DTC) still remains stored in the ECM. -
Page 142: Show Data When Trouble (Displaing Data At The Time Of Dtc)
FI SYSTEM DIAGNOSIS 4-27 SHOW DATA WHEN TROUBLE (DISPLAING DATA AT THE TIME OF DTC) ECM stores the engine and driving conditions (in the form of data as shown in the figure) at the moment of the detection of a malfunction in its memory. This data is called "Show data when trouble". Therefore, it is possible to know engine and driving conditions (e.g., whether the engine was warm or not, where the motorcycle was running or stopped) when a malfunction was detected by checking the show data when trouble. -
Page 143: Malfunction Code And Defective Condition
4-28 FI SYSTEM DIAGNOSIS MALFUNCTION CODE AND DEFECTIVE CONDITION DETECTED DTC No. DETECTED FAILURE CONDITION CHECK FOR ITEM NO FAULT ––––––––––– ––––––––––– CKP sensor The signal does not reach ECM for 3 CKP sensor wiring and mechan- sec. or more, after receiving the starter ical parts signal. - Page 144 FI SYSTEM DIAGNOSIS 4-29 DETECTED DTC No. DETECTED FAILURE CONDITION CHECK FOR ITEM Ignition CKP sensor (pick-up coil) signal is pro- Ignition coil, wiring/coupler con- signal duced, but signal from ignition coil is nection, power supply from the interrupted 8 times or more continu- battery ously.
-
Page 145: 12" (P0335) Ckp Sensor Circuit Malfunction
4-30 FI SYSTEM DIAGNOSIS "12" (P0335) CKP SENSOR CIRCUIT MALFUNCTION DETECTED CONDITION POSSIBLE CAUSE The signal does not reach ECM for 3 sec. or more, • Metal particles or foreign material being stuck on after receiving the starter signal. the CKP sensor and rotor tip •... - Page 146 FI SYSTEM DIAGNOSIS 4-31 5) If OK, then check the continuity between each terminal and ground. $ CKP sensor continuity: ∞ Ω (Infinity) (W – Ground) (G – Ground) ! 09900-25008: Multi-circuit tester set % Tester knob indication: Resistance (Ω) Are the resistance and continuity OK? Go to step 2.
- Page 147 4-32 FI SYSTEM DIAGNOSIS Is the voltage OK? ECM coupler (Harness side) • W or B wire open or shorted to ground. • Loose or poor contacts on the CKP sensor cou- pler or ECM coupler (terminal 6 or J). •...
-
Page 148: 13" (P0105-H/L) Iap Sensor Circuit Malfunction
FI SYSTEM DIAGNOSIS 4-33 "13" (P0105-H/L) IAP SENSOR CIRCUIT MALFUNCTION DETECTED CONDITION POSSIBLE CAUSE IAP sensor voltage is not within the fol- • Clogged vacuum passage between throttle body lowing range. and IAP sensor. 0.5 V Sensor voltage < 4.85 V •... - Page 149 4-34 FI SYSTEM DIAGNOSIS 4) Disconnect the IAP sensor coupler. 5) Turn the ignition switch ON. 6) Measure the voltage at the O/Bl wire and ground. 7) If OK, then measure the voltage at the O/Bl wire A and B wire B.
- Page 150 FI SYSTEM DIAGNOSIS 4-35 6) Disconnect the ECM coupler. 7) Check the continuity between P wire C and terminal H. 8) If OK, then check the continuity between B wire B and termi- nal J. $ IAPS lead wire continuity: Continuity (() ! 09900-25008: Multi-circuit tester set 09900-25009: Needle pointed probe set ) Tester knob indication: Continuity test (()
- Page 151 4-36 FI SYSTEM DIAGNOSIS 7) Disconnect the ECM coupler. 8) Check the continuity between O/Bl wire A and terminal 9. 9) Also, check the continuity between P wire C and terminal H. $ IAPS lead wire continuity: Continuity (() ! 09900-25008: Multi-circuit tester set 09900-25009: Needle pointed probe set ) Tester knob indication: Continuity test (() ECM coupler (Harness side)
- Page 152 FI SYSTEM DIAGNOSIS 4-37 Step 3 1) Turn the ignition switch OFF. 2) Remove the IAP sensor. 3) Connect the vacuum pump gauge to the vacuum port of the IAP sensor. Arrange 3 new 1.5 V batteries in series 1 (check that total voltage is 4.5 –...
-
Page 153: 14" (P0120-H/L) Tp Sensor Circuit Malfunction
4-38 FI SYSTEM DIAGNOSIS "14" (P0120-H/L) TP SENSOR CIRCUIT MALFUNCTION DETECTED CONDITION POSSIBLE CAUSE Output voltage is not within the following • TP sensor maladjusted range. • TP sensor circuit open or short Difference between actual throttle open- • TP sensor malfunction ing and opening calculated by ECM is •... - Page 154 FI SYSTEM DIAGNOSIS 4-39 4) Disconnect the TP sensor coupler. 5) Turn the ignition switch ON. 6) Measure the voltage at the O/Bl wire B and ground. 7) If OK, then measure the voltage at the O/Bl wire B and B wire C.
- Page 155 4-40 FI SYSTEM DIAGNOSIS 6) Disconnect the ECM coupler. 7) Check the continuity between Br wire A and terminal I. 8) Also, check the continuity between B wire C and terminal J. $ TPS lead wire continuity: Continuity (() ! 09900-25008: Multi-circuit tester set 09900-25009: Needle pointed probe set ) Tester knob indication: Continuity test (() ECM coupler (Harness side)
- Page 156 FI SYSTEM DIAGNOSIS 4-41 7) Disconnect the ECM coupler. 8) Check the continuity between Br wire A and terminal I. 9) Also, check the continuity between O/Bl wire B and terminal $ TPS lead wire continuity: Continuity (() ! 09900-25008: Multi-circuit tester set 09900-25009: Needle pointed probe set ) Tester knob indication: Continuity test (() ECM coupler (Harness side)
- Page 157 4-42 FI SYSTEM DIAGNOSIS Is the voltage OK? ECM coupler (Harness side) • Br, O/Bl or B wire open or shorted to ground, or poor I, 9 or J connection • If wire and connection are OK, intermittent trou- ble or faulty ECM. •...
-
Page 158: 15" (P0115-H/L) Ect Sensor Circuit Malfunction
FI SYSTEM DIAGNOSIS 4-43 "15" (P0115-H/L) ECT SENSOR CIRCUIT MALFUNCTION DETECTED CONDITION POSSIBLE CAUSE Output voltage is not within the following • ECT sensor circuit open or short range. • ECT sensor malfunction 0.15 V Sensor voltage < 4.85 V •... - Page 159 4-44 FI SYSTEM DIAGNOSIS Step 1 (When indicating P0115-H:) 1) Turn the ignition switch OFF. 2) Remove the frame covers. (#8-9) 3) Check the ECT sensor coupler 1 for loose or poor contacts. If OK, then check the ECT sensor lead wire continuity. 4) Disconnect the ECT sensor coupler and ECM coupler.
- Page 160 FI SYSTEM DIAGNOSIS 4-45 Step 1 (When indicating P0115-L:) 1) Turn the ignition switch OFF. 2) Remove the frame covers. (#8-9) 3) Check the ECT sensor coupler 1 for loose or poor contacts. If OK, then measure the output voltage. 4) Disconnect the ECT sensor coupler.
- Page 161 4-46 FI SYSTEM DIAGNOSIS Step 2 1) Turn the ignition switch OFF. 2) Disconnect the ECT sensor coupler. 3) Measure the ECT sensor resistance. $ ECT sensor resistance: Approx. 2.45 kΩ at 20 °C (Terminal – Terminal) ! 09900-25008: Multi-circuit tester set % Tester knob indication: Resistance (Ω) Refer to page 7-10 for details.
-
Page 162: 23" (P1651-H/L) To Sensor Circuit Malfunction
FI SYSTEM DIAGNOSIS 4-47 "23" (P1651-H/L) TO SENSOR CIRCUIT MALFUNCTION DETECTED CONDITION POSSIBLE CAUSE The sensor voltage should be the follow- • TO sensor circuit open or short ing for 2 sec. and more, after ignition • TO sensor malfunction switch is turned ON. - Page 163 4-48 FI SYSTEM DIAGNOSIS Step 1 (When indicating P1651-H:) 1) Turn the ignition switch OFF. 2) Remove the front leg shield. (#8-6) 3) Check the TO sensor coupler 1 for loose or poor contacts. If OK, then check the TO sensor lead wire continuity. 4) Disconnect the TO sensor coupler.
- Page 164 FI SYSTEM DIAGNOSIS 4-49 Step 1 (When indicating P1651-L:) 1) Turn the ignition switch OFF. 2) Remove the front leg shield. (#8-6) 3) Check the TO sensor coupler 1 for loose or poor contacts. If OK, then check the TO sensor lead wire continuity. 4) Disconnect the TO sensor coupler.
-
Page 165: 24" (P0351) Ignition System Malfunction
4-50 FI SYSTEM DIAGNOSIS Step 2 1) Connect the TO sensor coupler and ECM coupler. 2) Insert the needle pointed probes to the lead wire coupler. 3) Turn the ignition switch ON. 4) Measure the voltage between Lg and B wires. $ TO sensor voltage (Normal): 0.4 –... -
Page 166: 32" (P0201) Fuel Injector Circuit Malfunction
FI SYSTEM DIAGNOSIS 4-51 "32" (P0201) FUEL INJECTOR CIRCUIT MALFUNCTION DETECTED CONDITION POSSIBLE CAUSE CKP signal is produced but fuel injector signal is • Injector circuit open or short interrupted by 4 times or more continuously. • Injector malfunction • ECM malfunction Fuel pump speedometer Main relay... - Page 167 4-52 FI SYSTEM DIAGNOSIS 5) If OK, then check the continuity between each terminal and ground. $ Injector continuity: ∞ Ω (Infinity) ! 09900-25008: Multi-circuit tester set % Tester knob indication: Resistance (Ω) Are the resistance and continuity OK? Go to Step 2. Replace the injector with a new one.
-
Page 168: 40" (P0505 Or P0506 And P0507) Isc Valve Circuit Malfunction
FI SYSTEM DIAGNOSIS 4-53 "40" (P0505 or P0506 and P0507) ISC VALVE CIRCUIT MALFUNCTION DETECTED CONDITION POSSIBLE CAUSE The circuit voltage of motor drive is • ISC valve circuit open or shorted to ground (P0505) unusual. • Power source circuit open Idle speed is higher than the normal •... - Page 169 4-54 FI SYSTEM DIAGNOSIS 4) Disconnect the ISC valve coupler and ECM coupler. 5) Check the continuity between terminals A and 0, terminals B and M, terminals C and K, terminals D and 8. " When using the multi-circuit tester, do not strongly touch the terminal of the ECM coupler with a needle pointed tester probe to prevent the terminal damage or terminal bend.
- Page 170 FI SYSTEM DIAGNOSIS 4-55 ACTIVE CONTROL INSPECTION (ISC RPM CONTROL) Check 1 1) Set up the SDS tool. (Refer to the SDS operation manual for further details.) 2) Check that the engine is running. 3) Make sure that the engine coolant temperature on data moni- tor is indicated 70°C or more.
- Page 171 4-56 FI SYSTEM DIAGNOSIS Check 3 1) Click the button 1 and increase the "Spec" 2 to 1 650 rpm slowly. 2) Check that the "Desired idle speed" 3 is nearly equal to the "Spec" 2. Also, check that the number of steps 4 in the ISC valve position increases Check 4 1) Increase the "Spec"...
-
Page 172: 41" (P0230-H/L) Fp Circuit Malfunction
FI SYSTEM DIAGNOSIS 4-57 "41" (P0230-H/L) FP CIRCUIT MALFUNCTION DETECTED CONDITION POSSIBLE CAUSE No voltage is applied to fuel pump • Main relay circuit open or short although main relay is turned ON, or • Main relay malfunction voltage is applied to fuel pump, although •... - Page 173 4-58 FI SYSTEM DIAGNOSIS Is the main relay OK? ECM coupler (Harness side) • O/W or Y/W wire open or short or poor L con- nection • If wire and connection are OK, intermittent trou- ble or faulty ECM. • Recheck each terminal and wire harness for open circuit and poor connection.
-
Page 174: 42" (P01650) Ig Switch Circuit Malfunction
FI SYSTEM DIAGNOSIS 4-59 Step 1 (When indicating P0230-L:) 1) Turn the ignition switch OFF. 2) Remove the front frame cover. (#8-8) 3) Check the fuel pump coupler for loose or poor contacts. If OK, then check the main relay. (#9-21) Is the main relay OK? ECM coupler (Harness side) •... -
Page 175: 44" (P0130) Ho2 Sensor (Ho2S) Circuit Malfunction
4-60 FI SYSTEM DIAGNOSIS "44" (P0130) HO2 SENSOR (HO2S) CIRCUIT MALFUNCTION DETECTED CONDITION POSSIBLE CAUSE HO2 sensor output voltage is not input • HO2 sensor circuit open or shorted to ground. (P0130) to ECM during engine operation and • Fuel system malfunction. running condition. - Page 176 FI SYSTEM DIAGNOSIS 4-61 7) Disconnect the ECM coupler. 8) Check the continuity between Bl wire (harness side) and ter- minal E. 9) Also, check the continuity between B wire (harness side) and terminal J. $ HO2S lead wire continuity: Continuity (() ! 09900-25008: Multi-circuit tester set 09900-25009: Needle pointed probe set ECM coupler (Harness side)
- Page 177 4-62 FI SYSTEM DIAGNOSIS Is the voltage OK? ECM coupler (Harness side) • Bl wire or B wire open or shorted to ground, or poor E or J connection. • If wire and connection are OK, intermittent trou- ble or faulty ECM. •...
-
Page 178: Sensors
FI SYSTEM DIAGNOSIS 4-63 SENSORS CKP SENSOR INSPECTION The crankshaft position sensor is installed behind the generator cover. (#4-30) CKP SENSOR REMOVAL AND INSTALLATION • Remove the generator cover. (#3-14) • Install the generator cover in the reverse order of removal. IAP SENSOR INSPECTION The intake air pressure sensor is installed on the throttle body. -
Page 179: To Sensor Inspection
4-64 FI SYSTEM DIAGNOSIS TO SENSOR INSPECTION TO SENSOR REMOVAL AND INSTALLATION The tip-over sensor is located inside the front leg shield. (#4-47) • Remove the TO sensor. • Install the TO sensor in the reverse order of removal. NOTE: When installing the TO sensor, the arrow mark must be pointed upward. -
Page 180: Fuel System And Throttle
FUEL SYSTEM AND THROTTLE BODY FUEL SYSTEM AND THROTTLE BODY CONTENTS FUEL SYSTEM..................... 5- 2 CONSTRUCTION .................. 5- 2 REMOVAL AND DISASSEMBLY............5- 3 FUEL TANK REASSEMBLY AND INSTALLATION ......5- 5 FUEL PRESSURE INSPECTION ............5- 6 FUEL PUMP INSPECTION..............5- 7 FUEL DISCHARGE AMOUNT INSPECTION........ -
Page 181: Fuel System
FUEL SYSTEM AND THROTTLE BODY FUEL SYSTEM CONSTRUCTION " 1 Fuel tank 3 Cushion 2 O-ring A Fuel pump retainer ITEM N·m kgf-m... -
Page 182: Removal And Disassembly
FUEL SYSTEM AND THROTTLE BODY REMOVAL AND DISASSEMBLY • Remove the engine. (#3-3) • Remove the footboard. (#8-12) • Disconnect the fuel pump/fuel level gauge coupler 1. * Gasoline is highly flammable and explosive. * Keep heat, spark and flame away. •... - Page 183 FUEL SYSTEM AND THROTTLE BODY • Remove the fuel feed hose 6. • Loosen the fuel pump retainer using the special tool. % 09941-51012: Ring lock-nut wrench • Remove the fuel pump assembly. • Fuel pump inspection (#5-7 and 9-29)
-
Page 184: Fuel Tank Reassembly And Installation
FUEL SYSTEM AND THROTTLE BODY FUEL TANK REASSEMBLY AND INSTALLATION Reassemble and install the fuel tank in the reverse order of removal and disassembly. Pay attention to the following points: • Apply thin coat of the engine oil to the O-ring 1. Replace the gasket with a new one. -
Page 185: Fuel Pressure Inspection
FUEL SYSTEM AND THROTTLE BODY FUEL PRESSURE INSPECTION • Remove the front frame cover. (!8-11) • Place a rag under the fuel feed hose 1 and disconnect the fuel feed hose 1 from the fuel tank. • Install the special tools to the fuel tank. "... -
Page 186: Fuel Pump Inspection
FUEL SYSTEM AND THROTTLE BODY FUEL PUMP INSPECTION Turn the ignition switch ON and check that the fuel pump operates for a few seconds. If the fuel pump motor does not make operating sound, inspect the fuel pump circuit connections or inspect the main relay and tip-over sensor. -
Page 187: Fuel Mesh Filter Inspection And Cleaning
FUEL SYSTEM AND THROTTLE BODY FUEL MESH FILTER INSPECTION AND CLEANING • Remove the fuel pump assembly. (#5-3) • Remove the fuel mesh filter 1. • If the fuel mesh filter is clogged with sediment or rust, fuel will not flow smoothly and loss in engine power may result. •... -
Page 188: Throttle Body
FUEL SYSTEM AND THROTTLE BODY THROTTLE BODY CONSTRUCTION " 1 O-ring 6 Vacuum hose 2 Fuel injector 7 Throttle body ITEM N·m kgf-m 3 Cushion seal 8 TP sensor 0.18 4 Intake pipe 9 Insulator 5 IAP sensor... -
Page 189: Removal And Disassembly
5-10 FUEL SYSTEM AND THROTTLE BODY REMOVAL AND DISASSEMBLY The throttle body is assembled precisely in factory. Do not disassemble it other than shown in this manual. • Remove the trunk box. (#8-11) • Remove the air cleaner box outlet tube 1. •... - Page 190 FUEL SYSTEM AND THROTTLE BODY 5-11 • Remove the O-ring B. • Remove the TP sensor C. • Remove the IAP sensor D. • Disconnect the vacuum hose E. • Remove the fuel injector F. • Remove the intake pipe G.
-
Page 191: Inspection
5-12 FUEL SYSTEM AND THROTTLE BODY The ISC valve A is available only as the throttle body assembly. Never remove the throttle valve B. Avoid removing the throttle stop screw C. The throttle stop screw C is factory-adjusted at the time of delivery and therefore avoid removing or turn- ing it unless otherwise necessary. -
Page 192: Reassembly And Installation
* Align the throttle shaft end A with the groove B of TP sensor. * Apply grease to the throttle shaft end A if necessary. * Make sure the throttle valve open or close smoothly. ' 99000-25010: SUZUKI SUPER GREASE "A" or equivalent " TP sensor mounting screw: 1.8 N·m (0.18 kgf-m) •... -
Page 193: Exhaust System
EXHAUST SYSTEM EXHAUST SYSTEM CONTENTS EXHAUST SYSTEM ..................6- 2 REMOVAL ....................6- 2 INSPECTION ..................6- 3 INSTALLATION..................6- 3... - Page 194 EXHAUST SYSTEM EXHAUST SYSTEM REMOVAL To avoid the danger of being burned, do not touch the exhaust system when the system is hot. Any service on the exhaust system should be performed when the system is cool. " Make sure that the exhaust pipe and muffler have enough clearance from the rubber parts and plastic parts to avoid melting.
- Page 195 EXHAUST SYSTEM INSPECTION HO2 SENSOR (#4-60) INSTALLATION Install the exhaust pipe and muffler in the reverse order of removal. Pay attention to the following points: • Apply gas sealer to the muffler connector 1. EXHAUST GAS SEALER: PERMATEX 1372 (commercially available) "...
-
Page 196: Cooling And Lubrication
COOLING AND LUBRICATION SYSTEM COOLING AND LUBRICATION SYSTEM CONTENTS ENGINE COOLANT ..................7- 2 RADIATOR AND RADIATOR HOSE ............7- 3 INSPECTION ..................7- 3 REMOVAL ..................... 7- 4 DISASSEMBLY ..................7- 5 REASSEMBLY AND INSTALLATION ..........7- 5 COOLING FAN..................... 7- 7 INSPECTION .................. -
Page 197: Engine Coolant
COOLING AND LUBRICATION SYSTEM ENGINE COOLANT At the time of manufacture, the cooling system is filled with a 50:50 mixture of distilled water and ethylene glycol anti-freeze. This 50:50 mixture will provide the optimum corrosion protection and excellent heat pro- tection, and will protect the cooling system from freezing at temperatures above –31 °C (–24 °F). -
Page 198: Radiator And Radiator Hose
COOLING AND LUBRICATION SYSTEM RADIATOR AND RADIATOR HOSE INSPECTION Before removing the radiator and draining the engine coolant, inspect cooling system for tightness. • Remove the lid. • Remove the radiator cap and connect the tester 1 to the filler. •... -
Page 199: Removal
COOLING AND LUBRICATION SYSTEM REMOVAL • Remove the lower leg shield. ($8-7) • Remove the rear lower leg shield. ($8-8) • Place a container under the radiator hose. • Remove the radiator cap. " Do not remove the radiator cap when the radiator is hot. -
Page 200: Disassembly
COOLING AND LUBRICATION SYSTEM DISASSEMBLY • Remove the cooling fan 1. • Remove the cooling fan thermo-switch 2. RADIATOR INSPECTION AND CLEANING • Check the radiator for dirt or small bug stuck between the fins. • Use compressed air for cleaning. If dirt is excessive, wash with water. - Page 201 COOLING AND LUBRICATION SYSTEM RADIATOR • Connect the cooling fan thermo-switch coupler 1 and the cooling fan lead wire coupler 2. • Clamp the cooling fan thermo-switch lead wire and cooling fan lead wire with the frame. • With the hooked part A connected to the radiator end, install the radiator.
-
Page 202: Cooling Fan
COOLING AND LUBRICATION SYSTEM COOLING FAN INSPECTION • Remove the lower leg shield. ($8-7) • Remove the clamp. • Disconnect the cooling fan lead wire coupler 1. • Test the cooling fan motor for load current with an ammeter connected as shown in the illustration. •... -
Page 203: Cooling Fan Thermo-Switch
COOLING AND LUBRICATION SYSTEM COOLING FAN THERMO-SWITCH REMOVAL • Remove the lower leg shield. ($8-7) • Drain engine coolant. ($2-12) • Remove the clamp. • Disconnect the cooling fan thermo-switch coupler 1. • Remove the cooling fan thermo-switch 2. INSPECTION •... -
Page 204: Engine Coolant Temperature Gauge
COOLING AND LUBRICATION SYSTEM ENGINE COOLANT TEMPERATURE GAUGE REMOVAL • Remove the frame covers. ($8-10) • Disconnect the lead wire 1. • Remove the engine coolant temperature gauge 2. INSPECTION • Connect the engine coolant temperature gauge to the ohm- meter and dip it in water contained in a pan which is placed on an electric heater. -
Page 205: Ect Sensor
7-10 COOLING AND LUBRICATION SYSTEM ECT SENSOR REMOVAL • Remove the frame covers. ($8-10) • Remove the thermostat case. ($7-11) • Disconnect the ECT sensor coupler 1. • Remove the ECT sensor 2. INSPECTION • Check the ECT sensor by testing it at the bench as shown in the figure. -
Page 206: Installation
COOLING AND LUBRICATION SYSTEM 7-11 INSTALLATION • Tighten the ECT sensor to the specified torque. % ECT sensor: 18 N·m (1.8 kgf-m) * Replace the removed sealing washer 1 with a new one. * Take special care when handling the ECT sensor. It may cause damage if it gets a sharp impact. -
Page 207: Installation
7-12 COOLING AND LUBRICATION SYSTEM • Immerse the thermostat in water contained in a pan as shown and measure the valve start-to-open temperature when water is heated gradually. If the thermostat valve opening temperature is not within the specified range, replace the thermostat with a new one. # Thermostat valve opening temperature: Standard: Approx. -
Page 208: Water Pump
COOLING AND LUBRICATION SYSTEM 7-13 WATER PUMP REMOVAL AND DISASSEMBLY NOTE: Before draining engine oil and engine coolant, inspect engine oil and coolant leakage between the water pump and crankcase. If engine oil is leaking, visually inspect the oil seal and O-ring. If engine coolant is leaking, visually inspect the mechanical seal and seal washer. - Page 209 7-14 COOLING AND LUBRICATION SYSTEM • Remove the mechanical seal ring 0 and rubber seal A from the impeller. • Remove the mechanical seal B with the special tool. & 09921-20240: Bearing remover set (10 mm) NOTE: If there is no abnormal condition, the mechanical seal removal is not necessary.
-
Page 210: Inspection
• Install the oil seal with the special tool. & 09913-70210: Bearing installer set (22 mm) NOTE: The stamped mark on the oil seal faces mechanical seal side. • Apply a small quantity of grease to the oil seal lip. ( 99000-25010: SUZUKI SUPER GREASE "A" or equivalent... - Page 211 7-16 COOLING AND LUBRICATION SYSTEM • Install the new mechanical seal using a suitable size socket wrench. NOTE: On the new mechanical seal, the sealer A has been applied. • Install the rubber seal 1 into the impeller. • After wiping off the oily or greasy matter from the mechanical seal ring, install it into the impeller.
- Page 212 NOTE: * Apply engine coolant to the O-ring 3, 5. * Apply grease to the O-ring 4. ( 99000-25010: SUZUKI SUPER GREASE "A" or equivalent • Install the water pump assembly. Align the boss A of the water pump shaft end with the slot B of the oil pump shaft.
-
Page 213: Lubrication System
7-18 COOLING AND LUBRICATION SYSTEM LUBRICATION SYSTEM OIL PRESSURE $2-23 OIL FILTER $2-9 OIL SUMP FILTER $3-35 OIL PUMP $3-35... -
Page 214: Engine Lubrication System Chart
COOLING AND LUBRICATION SYSTEM 7-19 ENGINE LUBRICATION SYSTEM CHART EXHAUST ROCKER ARM EXHAUST ROCKER ARM SHAFT INTAKE ROCKER ARM CAM FACES INTAKE ROCKER ARM SHAFT CAM CHAIN CRANK PIN CAMSHAFT CAMSHAFT JOURNAL BEARING CYLINDER HEAD STARTER PISTON CLUTCH CYLINDER OIL NOZZLE CRANKSHAFT OIL FILTER MAIN GALLERY... - Page 215 CHASSIS CHASSIS CONTENTS EXTERIOR PARTS ..................8- 3 FASTENER .................... 8- 3 HANDLEBAR COVERS ................ 8- 4 FRONT COVER ..................8- 4 WINDSCREEN ..................8- 4 LOWER METER PANEL ............... 8- 5 FRONT LEG SHIELD ................8- 6 LOWER LEG SHIELD ................8- 7 SIDE LEG SHIELD (LH) ................
- Page 216 CHASSIS CHASSIS CONTENTS REAR WHEEL....................8-35 CONSTRUCTION .................. 8-35 REMOVAL ..................... 8-36 INSPECTION ..................8-36 INSTALLATION ..................8-36 FRONT BRAKE.................... 8-37 CONSTRUCTION .................. 8-37 BRAKE FLUID REPLACEMENT............8-38 BRAKE PAD REPLACEMENT.............. 8-38 FRONT BRAKE CALIPER REMOVAL AND DISASSEMBLY....8-38 FRONT BRAKE CALIPER INSPECTION ..........8-40 FRONT BRAKE CALIPER REASSEMBLY ..........
-
Page 217: Exterior Parts
CHASSIS EXTERIOR PARTS FASTENER REMOVAL • Depress the head of fastener center piece 1. • Pull out the fastener. INSTALLATION • Let the center piece stick out toward the head so that the pawls 2 close. • Insert the fastener into the installation hole. NOTE: To prevent the pawl 2 from damage, insert the fastener all the way into the installation hole. -
Page 218: Handlebar Covers
CHASSIS HANDLEBAR COVERS REMOVAL • Remove the rear view mirrors 1 and fasteners. • Remove the rear handlebar cover 2 by pulling it upward. • Remove the front handlebar cover 3. INSTALLATION Installation is in the reverse order of removal. FRONT COVER REMOVAL Remove the screws. -
Page 219: Lower Meter Panel
CHASSIS LOWER METER PANEL REMOVAL • Remove the windscreen. ("8-4) • Remove the screw 1. • Remove the lower meter panel 2 by removing the speedom- eter mounting screws. INSTALLATION Installation is in the reverse order of removal. -
Page 220: Front Leg Shield
CHASSIS FRONT LEG SHIELD REMOVAL • Remove the front cover. ("8-4) • Remove the floor mats 1. • Remove the screws (8 pcs) and fasteners (4 pcs). • Disconnect the coupler 2 and remove the front leg shield along with the headlight assembly. INSTALLATION Installation is in the reverse order of removal. -
Page 221: Lower Leg Shield
CHASSIS LOWER LEG SHIELD REMOVAL • Remove the front leg shield. ("8-6) • Remove the screws (6 pcs) and fasteners (4 pcs). • Remove the horn mounting bolt 1. • Remove the lower leg shield 2. Take care not to bend the radiator fins. INSTALLATION Installation is in the reverse order of removal. -
Page 222: Side Leg Shield (Rh)
CHASSIS SIDE LEG SHIELD (RH) REMOVAL • Remove the floor mat (RH). • Remove the battery cover 1. • Remove the side leg shield (RH) 2. INSTALLATION Installation is in the reverse order of removal. REAR LOWER LEG SHIELD REMOVAL •... -
Page 223: Seat
CHASSIS SEAT REMOVAL • Open the seat. • Remove the seat by removing the three nuts. INSTALLATION Installation is in the reverse order of removal. PILLION RIDER HANDLES REMOVAL • Open the seat. • Remove the pillion rider handles 1 (LH and RH). INSTALLATION Installation is in the reverse order of removal. - Page 224 8-10 CHASSIS • Remove the rear combination light 2, upper frame cover 3 and rear footboards 4 (LH and RH) from the frame covers 5 (LH and RH). INSTALLATION Installation is in the reverse order of removal.
-
Page 225: Trunk Box
CHASSIS 8-11 TRUNK BOX REMOVAL • Remove the frame covers. ("8-10) • Remove the main fuse 1, ECM 2, brake switch relay 3 and main relay 4 from the upper trunk box. NOTE: Do not disconnect the ECM and relay couplers. •... -
Page 226: Footboard
8-12 CHASSIS FOOTBOARD REMOVAL • Remove the front frame cover. ("8-8) • Remove the floor mats. • Remove the side leg shields. ("8-7 and -8) • Remove the frame covers. ("8-10) • Remove the battery and stater relay 1. • Remove the screws (6 pcs) and bolts (4 pcs). •... -
Page 227: Front Box
CHASSIS 8-13 FRONT BOX REMOVAL • Remove the windscreen. ("8-4) • Remove the handlebars. ("8-20) • Remove the front leg shield. ("8-6) • Remove the side leg shields. ("8-7 and -8) • Remove the frame covers. ("8-10) • Remove the footboard. ("8-12) •... -
Page 228: Front Wheel
8-14 CHASSIS FRONT WHEEL CONSTRUCTION 1 Brake disc 6 Speedometer gear box 2 Collar 7 Front axle ITEM N·m kgf-m 3 Dust seal A Front axle nut 4 Bearing B Brake disk bolt 5 Spacer... -
Page 229: Removal
CHASSIS 8-15 REMOVAL • Support the motorcycle with the center stand. • Remove the axle nut 1. • Lift the front wheel off the ground using a jack. * Make sure that the motorcycle is securely supported. * Do not operate the front brake lever while front wheel is removed. - Page 230 8-16 CHASSIS • Remove the dust seal 3. & 09913-50121: Oil seal remover The removed dust seal must be replaced with a new one. • Remove the bearing. & 09921-20240: Bearing remover set The removed bearing must be replaced with a new one.
-
Page 231: Reassembly And Installation
WHEEL BEARING • Apply grease to the wheel bearings. ' 99000-25010: SUZUKI SUPER GREASE "A" or equivalent • Install the wheel bearing with the special tool. • Insert the spacer and install the left bearing. - Page 232 • Apply grease to the dust seal lip. • Apply grease to the collar and install the collar straight to pre- vent the dust seal lip from damage. ' 99000-25010: SUZUKI SUPER GREASE "A" or equivalent SPEEDOMETER GEARBOX • Apply grease to the speedometer gear and dust seal lip.
-
Page 233: Handlebars
CHASSIS 8-19 HANDLEBARS CONSTRUCTION 1 Handlebars 5 Right handlebar switch box 2 Handlebar balancer 6 Throttle grip ITEM N·m kgf-m 3 Left grip rubber A Handlebar set bolt 4 Left handlebar switch box B Handlebar clamp nut... -
Page 234: Removal
8-20 CHASSIS REMOVAL • Remove the handlebar covers. ("8-4) • Remove the following items from the handlebars. 1 Handlebar balancer 2 Left handlebar switch box 3 Rear brake light switch lead wires 4 Rear brake master cylinder 5 Grip rubber 6 Handlebar balancer 7 Right handlebar switch box 8 Throttle grip... - Page 235 • Apply grease to the hatched area A before installing the throttle grip 1. A: 135 mm ' 99000-25010: SUZUKI SUPER GREASE "A" or equivalent • Insert the projection A of the right handlebar switch into the hole of the handlebar.
-
Page 236: Front Fork
8-22 CHASSIS FRONT FORK CONSTRUCTION 1 O-ring 8 Oil seal stopper ring 2 Front fork spring 9 Oil lock piece ITEM N·m kgf-m 3 Damper rod ring 0 Oil seal 4 Damper rod A Outer tube 5 Damper rod spring A Front fork cap bolt 6 Inner tube B Damper rod bolt... -
Page 237: Removal And Disassembly
CHASSIS 8-23 REMOVAL AND DISASSEMBLY • Remove the front leg shield. ("8-6) • Dismount the front wheel. ("8-15) • Remove the brake caliper and brake hose guide. • Remove the speed meter cable guide 1. Hang the brake caliper on the frame with a string etc., taking care not to bend the brake hose. - Page 238 8-24 CHASSIS • Remove the front fork spring 4 and drain front fork oil. • Remove the damper rod bolt using the special tools. & 09940-34520: T-Handle 09940-34531: Attachment (A) • Remove the inner tube 5 and oil lock piece 6 from the outer tube.
-
Page 239: Inspection
CHASSIS 8-25 • Remove the oil seal stopper ring 0. • Remove the oil seal A. & 09913-50121: Oil seal remover The removed oil seal must be replaced with a new one. INSPECTION FRONT FORK SPRING Measure the free length A of the front fork spring. If the length is found shorter than the service limit, replace the spring with a new one. -
Page 240: Reassembly
8-26 CHASSIS REASSEMBLY Reassemble and remount the front fork in the reverse order of removal and disassembly. Pay attention to the following points: * Thoroughly wash all the component parts being assembled. * When reassembling the front fork, use new fork oil. * Use the specified fork oil for the front fork. - Page 241 CHASSIS 8-27 STOPPER RING/DUST SEAL • Install the oil seal stopper ring 1 and dust seal 2. Make sure that the stopper ring is securely fitted into the groove on the outer tube. 1 Oil seal stopper ring 2 Dust seal 3 Oil seal 4 Slide metal FRONT FORK OIL...
- Page 242 8-28 CHASSIS • Insert the front fork inner tube top end into the steering stem all the way until the step of mounting hole has been con- tacted. • Tighten the clamp bolts temporarily. FRONT FORK CAP BOLT • Install new O-ring to the front fork cap bolt and apply fork oil. •...
-
Page 243: Steering
CHASSIS 8-29 STEERING CONSTRUCTION 1 Washer 6 Lower bearing 2 Steering stem nut 7 Steering stem ITEM N·m kgf-m 3 Upper bearing inner race 8 Lower bearing inner race 4 Dust cover A Steering stem lock nut 5 Upper bearing B Front fork clamp bolt... -
Page 244: Removal And Disassembly
8-30 CHASSIS REMOVAL AND DISASSEMBLY • Remove the front leg shield. ("8-6) • Remove the front forks. ("8-23) • Remove the front brake hose guide 1 and speedometer guide 2. • Remove the clamp 3. • Remove the handlebar set bolt 4 and clamp bolt 5. •... -
Page 245: Inspection And Disassembly
CHASSIS 8-31 INSPECTION AND DISASSEMBLY Check the steering stem and steering stem head for any dam- age. Check the bearings and races for corrosion, nick or other dam- age. If any abnormal condition is noted, replace the damaged part with a new one. •... -
Page 246: Reassembly
09940-51410: Attachment • Apply grease to the upper bearing and upper inner race prior to installing the steering stem. ' 99000-25010: SUZUKI SUPER GREASE "A" or equivalent • Install the upper bearing and upper inner races. • Apply grease to the lower bearing prior to installing the steer- ing stem. - Page 247 CHASSIS 8-33 • Tighten the steering stem nut. $ Steering stem nut: 45 N·m (4.5 kgf-m) & 09940-14911: Steering socket wrench 09940-11420: Steering stem nut socket 09940-11430: Steering stem nut socket • Turn the steering stem right and left 5 – 6 times to break-in the bearing.
- Page 248 8-34 CHASSIS • Tighten the handlebar set bolt 3 and handlebar clamp nut 4 to the specified torque. $ Handlebar set bolt: 25 N·m (2.5 kgf-m) Handlebar clamp nut: 50 N·m (5.0 kgf-m) Apply THREAD LOCK SUPER to the handlebar set bolt. * 99000-32110: THREAD LOCK SUPER "1322"...
-
Page 249: Rear Wheel
CHASSIS 8-35 REAR WHEEL CONSTRUCTION 1 Collar 4 Rear wheel 2 Spacer A Rear axle nut ITEM N·m kgf-m 3 Brake disc B Brake disk bolt 12.0... -
Page 250: Removal
8-36 CHASSIS REMOVAL • Support the motorcycle with the center stand. • Remove the muffler. ("6-2) • Remove the rear brake caliper 1. • Remove the rear axle nut 2 and collar. • Remove the rear swingarm 3. • Remove the spacer 4. •... -
Page 251: Front Brake
CHASSIS 8-37 FRONT BRAKE CONSTRUCTION 1 Diaphragm 0 Brake pad 2 Master cylinder A Pad spring ITEM N·m kgf-m 3 Piston/cup set A Master cylinder bolt (upper) 4 Delay valve B Master cylinder bolt (lower) 5 Brake caliper C Brake hose union bolt 6 Caliper bracket D Brake caliper mounting bolt 7 Piston seal... -
Page 252: Brake Fluid Replacement
8-38 CHASSIS * This brake system is filled with an ethylene glycol-based DOT 4 brake fluid. Do not use mix different types of fluid such as silicone-based or petroleum-based. * Do not use any brake fluid taken from old, used or unsealed containers. Never reuse brake fluid left over from the last servicing or stored for long periods. - Page 253 CHASSIS 8-39 • Remove the brake pad springs 4 and 5. • Using an air blow gun, pressurize the caliper fluid chamber to push out the pistons. • Blow the hole A to push out the center piston. • Blow the hole B to push out the upper and lower pistons. * Place a rag over the pistons to prevent them from popping out and keep hand off the pistons.
-
Page 254: Front Brake Caliper Inspection
8-40 CHASSIS FRONT BRAKE CALIPER INSPECTION Inspect the caliper cylinder wall and piston surface for scratch, corrosion or other damages. If any abnormal condition is noted, replace it with a new one. Inspect the caliper bracket 1 for any damage. Inspect the rubber boots 2 for any damage. - Page 255 CHASSIS 8-41 • Apply SUZUKI SILICONE GREASE to the caliper bracket pin 1 and boots 2. . 99000-25100: SUZUKI SILICONE GREASE or equivalent • Install the caliper bracket. • Install the brake pad springs 3 and 4 properly. • Install the brake pads.
-
Page 256: Brake Disc Inspection
8-42 CHASSIS BRAKE DISC INSPECTION Check the brake disc surface for scratch, crack or abnormal wear. Measure the disc thickness at several positions using a micrometer. If the measurement is less than the service limit or any abnormal condition is noted, replace the disc with a new one. (For replacement procedure: "8-16) % Brake disc thickness Service Limit: 4.0 mm... -
Page 257: Front Brake Master Cylinder Inspection
CHASSIS 8-43 • Remove the brake light switch 3 and brake lever 4. • Remove the dust boot 5. • Remove the snap ring 6. • Remove the washer 7 and piston/cup set 8. FRONT BRAKE MASTER CYLINDER INSPECTION Check the cylinder inside wall, piston/cup set and spring for scratch, corrosion or other abnormal condition. -
Page 258: Front Brake Master Cylinder Reassembly And Installation
- Specification and classification: DOT 4 • When installing the brake light switch, align the projection on the switch with the hole in the master cylinder. • Apply SUZUKI SILICONE GREASE to the brake lever pivot bolt. . 99000-25100: SUZUKI SILICONE GREASE or equivalent •... - Page 259 CHASSIS 8-45 • When installing the master cylinder onto the handlebars, align the master cylinder holder's mating surface A with the punch mark B on the handlebars and tighten the upper holder bolt first. A Mating surface B Punch mark C Master cylinder D Handlebars E Upper holder bolt...
-
Page 260: Rear Brake
8-46 CHASSIS REAR BRAKE CONSTRUCTION 1 Diaphragm A Caliper bracket 2 Master cylinder B Rear brake pipe ITEM N·m kgf-m 3 Piston/cup set *1 To the delay valve 4 Brake pad shim *2 To the rear brake caliper 5 Brake pads A Master cylinder bolt (upper) 6 Brake caliper B Master cylinder bolt (lower) -
Page 261: Rear Brake Caliper Removal And Disassembly
CHASSIS 8-47 * This brake system is filled with an ethylene glycol-based DOT 4 brake fluid. Do not use mix different types of fluid such as silicone-based or petroleum-based. * Do not use any brake fluid taken from old, used or unsealed containers. Never reuse brake fluid left over from the last servicing or stored for long periods. -
Page 262: Rear Brake Caliper Inspection
8-48 CHASSIS • Using an air blow gun, pressurize the caliper fluid chamber to push out the piston. * Place a rag over the piston to prevent it from pop- ping out and flying and keep hand off the piston. * Be careful of brake fluid which can possibly splash. -
Page 263: Rear Brake Master Cylinder Removal And Disassembly
CHASSIS 8-49 • Apply SUZUKI SILICONE GREASE to the caliper bracket pins. . 99000-25100: SUZUKI SILICONE GREASE or equivalent • Install the brake pads and brake pad bolts. $ Brake pad bolt: 18 N·m (1.8 kgf-m) • Tighten the brake caliper mounting bolts 1. -
Page 264: Rear Brake Master Cylinder Reassembly And Installation
8-50 CHASSIS REAR BRAKE MASTER CYLINDER REASSEMBLY AND INSTALLATION Reassemble and install the rear brake master cylinder in the same manner as the front one. ("8-44) DELAY VALVE REMOVAL • Drain brake fluid from the combination brake system. ("2-16) • Remove the front leg shield. ("8-6) •... -
Page 265: Rear Suspension
CHASSIS 8-51 REAR SUSPENSION CONSTRUCTION 1 Rear swingarm Rear shock absorber mounting 2 Dust seal bolt (Upper and lower) ITEM N·m kgf-m 3 Bearing 4 Rear shock absorber... -
Page 266: Rear Swingarm Bearing Inspection
& 09913-70210: Bearing installer set (40 mm) • Install new dust seal using the special tool. & 09913-70210: Bearing installer set (35 mm) • Apply grease to the lip of dust seal. ' 99000-25010: SUZUKI SUPER GREASE "A" or equivalent • Install the rear swingarm. ("8-36) -
Page 267: Rear Shock Absorber Removal
CHASSIS 8-53 REAR SHOCK ABSORBER REMOVAL • Remove the frame covers. ("8-9) • Remove the muffler for right rear shock absorber removal. ("6-2) • Move the air cleaner box upward for left rear shock absorber removal. ("2-10) • Remove the rear shock absorber. REAR SHOCK ABSORBER INSPECTION •... -
Page 268: Tire And Wheel
8-54 CHASSIS TIRE AND WHEEL TIRE REMOVAL The most critical factor of tubeless tire is the seal between the wheel rim and the tire bead. For this reason, it is recommended to use a tire changer that can satisfy this sealing requirement and can make the operation efficient as well as functional. -
Page 269: Valve Inspection
CHASSIS 8-55 VALVE INSPECTION • Inspect the valve after the tire is removed from the rim. • Replace the valve with a new one if the seal rubber A is peel- ing or has damage. NOTE: If the external appearance of the valve shows no abnormal con- dition, removing of the valve is not necessary. -
Page 270: Tire Installation
8-56 CHASSIS TIRE INSTALLATION • Apply tire lubricant to the tire bead. • When installing the tire onto the wheel, observe the following points. * Do not reuse the valve which has been once removed. * Never use oil, grease or gasoline on the tire bead in place of tire lubricant. - Page 271 CHASSIS 8-57 • In this condition, check the "rim line" B cast on the tire side walls. The line must be equidistant from the wheel rim all around. If the distance between the rim line and wheel rim varies, this indicates that the bead is not properly seated. If this is the case, deflate the tire completely and unseat the bead for both sides.
-
Page 272: Electrical System
ELECTRICAL SYSTEM ELECTRICAL SYSTEM CONTENTS CAUTIONS IN SERVICING ................. 9- 3 CONNECTOR ..................9- 3 COUPLER....................9- 3 CLAMP ....................9- 3 FUSE...................... 9- 3 SWITCH ....................9- 3 SEMI-CONDUCTOR EQUIPPED PART ..........9- 4 BATTERY ....................9- 4 CONNECTING THE BATTERY............. 9- 4 WIRING PROCEDURE................ - Page 273 ELECTRICAL SYSTEM ELECTRICAL SYSTEM CONTENTS LAMPS ......................9-30 HEADLIGHT, POSITION LIGHT, BRAKE LIGHT/TAILLIGHT, LICENSE PLATE LIGHT AND TURN SIGNAL LIGHT ......9-30 BULB REPLACEMENT................. 9-31 HEADLIGHT BEAM ADJUSTMENT ............. 9-34 SWITCHES ....................9-35 IGNITION SWITCH REMOVAL AND INSTALLATION ......9-35 INSPECTION ..................
-
Page 274: Cautions In Servicing
ELECTRICAL SYSTEM CAUTIONS IN SERVICING CONNECTOR • When connecting a connector, be sure to push it in until a click is felt. • Inspect the connector for corrosion, contamination and break- age in its cover. COUPLER Click • With a lock type coupler, be sure to release the lock when dis- connecting, and push in fully to engage the lock when con- necting. -
Page 275: Semi-Conductor Equipped Part
ELECTRICAL SYSTEM SEMI-CONDUCTOR EQUIPPED PART • Be careful not to drop the part with a semi-conductor built in INCORRECT such as a ECM. • When inspecting this part, follow inspection instruction strictly. Neglecting proper procedure may cause damage to this part. BATTERY •... -
Page 276: Using The Multi-Circuit Tester
ELECTRICAL SYSTEM USING THE MULTI-CIRCUIT TESTER • Properly use the multi-circuit tester + and - probes. Improper use can cause damage to the motorcycle and tester. • If the voltage and current values are not known, begin mea- suring in the highest range. •... -
Page 277: Location Of Electrical Components
ELECTRICAL SYSTEM LOCATION OF ELECTRICAL COMPONENTS 1 IAP sensor 9 CKP sensor 2 Fuel injector 0 Generator 3 ISC valve A HO2 sensor 4 Trunk light switch B Starter relay 5 Regulator/Rectifier C Battery D Cooling fan 6 Front brake switch E Cooling fan thermo-switch 7 Handlebar switch (RH) 8 Ignition switch... - Page 278 ELECTRICAL SYSTEM F TO sensor O TP sensor G Side-stand relay P Horn H Turn signal relay Q Fuse box I Handlebar switch (LH) R Side-stand switch J Combination brake switch S Fuel pump K Main fuse T Fuel level gauge L ECM U Engine coolant temperature gauge M Brake start relay...
-
Page 279: Charging System
ELECTRICAL SYSTEM CHARGING SYSTEM lgnition switch Main fuse Battery Regulator/Rectifier TROUBLESHOOTING Battery runs down quickly Step 1 1) Check accessories which use excessive amounts of electricity. Are accessories being installed? Remove accessories. Go to Step 2. Step 2 1) Check the battery for current leaks. (!9-10) Is the battery for current leaks OK? Go to Step 3. - Page 280 ELECTRICAL SYSTEM Step 4 1) Measure the resistance of the generator coil. (!9-11) Is the resistance of generator coil OK? Go to Step 5. • Faulty generator coil • Disconnected lead wires Step 5 1) Measure the generator no-load performance. (!9-11) Is the generator no-load performance OK? Go to Step 6.
-
Page 281: Inspection
9-10 ELECTRICAL SYSTEM INSPECTION BATTERY CURRENT LEAKAGE • Turn the ignition switch to the OFF position. • Remove the battery cover. (!8-8) • Disconnect the battery - lead wire. • Measure the current between battery - terminal and - lead wire using the multi-circuit tester. - Page 282 ELECTRICAL SYSTEM 9-11 GENERATOR COIL RESISTANCE • Remove the right side leg shield. (!8-8) • Disconnect the generator coupler 1. • Measure the resistance between the three lead wires. If the resistance is out of specified value, replace the stator with a new one.
- Page 283 9-12 ELECTRICAL SYSTEM Measure the voltage between the terminals using the multi-cir- cuit tester, as indicated in the table below. If the voltage is not within the specified value, replace the regu- lator/rectifier with a new one. " 09900-25008: Multi-circuit tester set ) Tester knob indication: Diode test (*) Unit: V - Tester prove...
-
Page 284: Starter System
ELECTRICAL SYSTEM 9-13 STARTER SYSTEM Main relay Engine To Fuel pump stop Side-stand relay switch 15 A 30 A Ignition switch Brake switch Side- stand switch Brake start relay Battery Starter relay Starter motor TROUBLE SHOOTING NOTE: Make sure the fuses are not blown and the battery is fully-charged before diagnosing. Starter motor will not run. -
Page 285: Starter Motor Removal
9-14 ELECTRICAL SYSTEM Step 3 1) Measure the starter relay voltage at the starter relay connectors (between Bl/W + and R/W -) when the starter button is pushed. Is a voltage OK? Go to Step 4. • Faulty safety relay. •... -
Page 286: Starter Motor Disassembly
ELECTRICAL SYSTEM 9-15 STARTER MOTOR DISASSEMBLY • Disassemble the starter motor as shown in the illustration. 1 O-ring 6 Starter motor case 2 Housing end (inside) 7 Armature ITEM N·m kgf-m 3 Oil seal 8 Housing end (outside) 4 Washer A Starter motor lead wire bolt 5 Shim B Starter motor mounting bolt... -
Page 287: Starter Motor Inspection
9-16 ELECTRICAL SYSTEM STARTER MOTOR INSPECTION CARBON BRUSH Inspect the brushes for abnormal wear, cracks, or smoothness in the brush holder. If any damages are found, replace the brush assembly with a new one. Make sure that the length A is not less than 3.5 mm. If this length becomes less than 3.5 mm, replace the brush. -
Page 288: Starter Motor Reassembly
• Apply grease to the bearing and lip of oil seal. . 99000-25010: SUZUKI SUPER GREASE "A" or equivalent • Apply a little SUZUKI MOLY PASTE to the armature shaft end. / 99000-25140: SUZUKI MOLY PASTE or equivalent To prevent oil or water from entering into the motor inside, the O-rings must be replaced with new ones. -
Page 289: Starter Motor Installation
9-18 ELECTRICAL SYSTEM STARTER MOTOR INSTALLATION • Apply grease to the O-ring 1. . 99000-25010: SUZUKI SUPER GREASE "A" or equivalent • Install the starter motor. • Tighten the starter motor mounting bolts 1 and lead wire screw 2 to the specified torque. -
Page 290: Starter Relay Inspection
ELECTRICAL SYSTEM 9-19 STARTER RELAY INSPECTION • Remove the battery cover and right side leg shield. (!8-8) • Disconnect the battery - lead wire from the battery. • Disconnect the starter motor read wire, battery + lead wire and starter relay coupler 1. •... -
Page 291: Side-Stand/Ignition Interlock System Parts Inspection
9-20 ELECTRICAL SYSTEM SIDE-STAND/IGNITION INTERLOCK SYSTEM PARTS INSPECTION Check the interlock system for proper operation. If the interlock system does not operate properly, check each component for damage or abnormalities. If any abnormality is found, replace the component with a new one. SIDE-STAND SWITCH INSPECTION •... - Page 292 ELECTRICAL SYSTEM 9-21 Check there is continuity between the terminals 2 and 3 when 12 V battery voltage is applied; positive to the terminal 4 and negative to the terminal 5. If no continuity is noted, the relay must be replaced. TURN SIGNAL RELAY INSPECTION •...
-
Page 293: Ignition System
9-22 ELECTRICAL SYSTEM IGNITION SYSTEM Engine stop switch Side-stand relay lgnition coil lgnition fuse sensor lgnition switch Main fuse Battery sensor sensor NOTE: The fuel cut-off circuit is incorporated in this ECM in order to prevent over-running of engine. When engine speed reaches 10 000 r/min, this circuit cuts off fuel at the fuel injector. - Page 294 ELECTRICAL SYSTEM 9-23 Step 2 1) Measure the battery voltage between input lead wires (R/W and B/W) at the ECM with the ignition switch in the "ON" position. Is the voltage OK? Go to Step 3. • Faulty ignition switch. •...
-
Page 295: Inspection
9-24 ELECTRICAL SYSTEM INSPECTION IGNITION COIL PRIMARY PEAK VOLTAGE • Remove the front frame cover. (!8-8) • Disconnect spark plug cap. • With the spark plug cap connected, place a new spark plug on the engine to ground it. NOTE: * Check that all the couplers are connected. - Page 296 ELECTRICAL SYSTEM 9-25 IGNITION COIL RESISTANCE • Remove the front frame cover. (!8-8) • Disconnect the ignition coil read wires. Measure the ignition coil resistance in both the primary and sec- ondary windings. If the resistance is not within the standard range, replace the ignition coil with a new one.
- Page 297 9-26 ELECTRICAL SYSTEM CKP SENSOR RESISTANCE CKP Sensor • Measure the resistance between the lead wires and ground. If coupler the resistance is not as specified, the CKP sensor must be replaced. $ CKP sensor resistance: 158 – 238 Ω (W – G) ∞...
-
Page 298: Combination Meter
ELECTRICAL SYSTEM 9-27 COMBINATION METER REMOVAL AND DISASSEMBLY • Remove the speedometer. (!8-5) • Disassemble the speedometer, as shown. When disconnecting and reconnecting the speedome- ter coupler, make sure to turn OFF the ignition switch, or electronic parts may get damaged. -
Page 299: Inspection
9-28 ELECTRICAL SYSTEM INSPECTION WATER TEMPERATURE METER • Remove the frame covers. (!8-9) • Disconnect the water temperature switch lead wire 1. • With the ignition switch turned on and a variable resister con- nected between the B/G lead wire and ground check for the water temperature meter needle indication when the resis- tance is adjusted to the specified values. - Page 300 ELECTRICAL SYSTEM 9-29 FUEL LEVEL GAUGE INSPECTION Measure resistance between the terminals when the float is at the position instead below. " 09900-25008: Multi-circuit tester set Fuel float position Resistance between terminals F:96.6 mm from Approx. 10 Ω tank mating face 1/2:154.6 mm from Approx.
-
Page 301: Lamps
9-30 ELECTRICAL SYSTEM LAMPS HEADLIGHT, POSITION LIGHT, BRAKE LIGHT/TAILLIGHT, LICENSE PLATE LIGHT AND TURN SIGNAL LIGHT HEADLIGHT 12 V 55 W 1 × 2 POSITION LIGHT 12 V 5 W 2 × 2 TURN SIGNAL Front: 12 V 21 W 3 × 2 BRAKE LIGHT/TAILLIGHT 12 V 21/5 W 4 ×... -
Page 302: Bulb Replacement
ELECTRICAL SYSTEM 9-31 BULB REPLACEMENT HEADLIGHT • Remove the front leg shield. (!8-6) • Remove the headlight bulb terminals 1 and rubber boot 2. • Remove the headlight bulb by unhooking the bulb holder spring 3. • Install new bulb and reassemble the headlight in the reverse order of the above procedure. - Page 303 9-32 ELECTRICAL SYSTEM FRONT TURN SIGNAL LIGHT • Remove the front leg shield. (!8-6) • Turn the socket counterclockwise and remove it. • Replace the bulb with a new one. • Reinstall the socket and front leg shield in the reverse order of removal.
- Page 304 ELECTRICAL SYSTEM 9-33 BRAKE LIGHT/TAILLIGHT • Remove the lower frame cover. (!8-9) • Move the rear fender downward. • Turn the socket counterclockwise and remove it. • Replace the bulb with a new one. • Reinstall the socket and lower frame cover in the reverse order of removal.
-
Page 305: Headlight Beam Adjustment
9-34 ELECTRICAL SYSTEM • Replace the bulb with a new one. • Reinstall the lens. HEADLIGHT BEAM ADJUSTMENT The headlight beam can be adjusted vertically if necessary. • Turn the adjuster 1 clockwise or counterclockwise with a screwdriver. -
Page 306: Switches
ELECTRICAL SYSTEM 9-35 SWITCHES IGNITION SWITCH REMOVAL AND INSTALLATION REMOVAL • Remove the front leg shield. (!8-6) • Remove the right inner front box 1. • Remove the torx bolt and nut. " 09930-11930: Torx bit (JT30H) 09930-11940: Bit holder •... -
Page 307: Inspection
9-36 ELECTRICAL SYSTEM INSPECTION Check for continuity between each terminal. If any abnormal condition is noted, replace the switch. " 09900-25008: Multi-circuit tester IGNITION SWITCH FRONT BRAKE SWITCH Color Color B/Bl Position Position LOCK COMBINATION BRAKE SWITCH DIMMER SWITCH Color Position Color Position... -
Page 308: Battery
ELECTRICAL SYSTEM 9-37 BATTERY SPECIFICATIONS Type designation GTX9-BS Capacity 12 V, 28.8 kC (8 Ah)/10 HR 1 Upper cover breather 5 Terminal 2 Cathode plates 6 Safety valve 3 Stopper 7 Anode plates 4 Filter 8 Separator (Fiberglass plate) INITIAL CHARGING Filling electrolyte •... - Page 309 9-38 ELECTRICAL SYSTEM NOTE: If no air bubbles are coming up from a filler port, tap the bottom of the electrolyte container two or three times. Never remove the container from the battery. • After confirming that the electrolyte has entered the battery completely, remove the electrolyte containers from the bat- tery.
-
Page 310: Servicing
ELECTRICAL SYSTEM 9-39 SERVICING Visually inspect the surface of the battery container. If any signs of cracking or electrolyte leakage from the sides of the battery have occurred, replace the battery with a new one. If the battery terminals are found to be coated with rust or an acidic white powdery substance, clean the battery terminals with sandpaper. -
Page 311: Servicing Information
SERVICING INFORMATION 10-1 SERVICING INFORMATION CONTENTS TROUBLESHOOTING ................10- 2 FI SYSTEM MALFUNCTION CODE AND DEFECTIVE CONDITION..............10- 2 ENGINE ....................10- 4 RADIATOR (COOLING SYSTEM) ............10- 9 CHASSIS ..................... 10-10 BRAKES ....................10-11 ELECTRICAL ..................10-12 BATTERY .................... 10-13 WIRING DIAGRAM .................. -
Page 312: Troubleshooting
10-2 SERVICING INFORMATION TROUBLESHOOTING FI SYSTEM MALFUNCTION CODE AND DEFECTIVE CONDITION DETECTED DTC No. DETECTED FAILURE CONDITION CHECK FOR ITEM NO FAULT ––––––––––– ––––––––––– CKP sensor The signal does not reach ECM for 3 CKP sensor wiring and mechan- sec. or more, after receiving the starter ical parts signal. - Page 313 SERVICING INFORMATION 10-3 DETECTED DTC No. DETECTED FAILURE CONDITION CHECK FOR ITEM TO sensor The sensor voltage should be the fol- TO sensor, lead wire/coupler lowing for 2 sec. and more, after igni- connection tion switch is turned ON. 0.2 V sensor voltage <...
-
Page 314: Engine
10-4 SERVICING INFORMATION DETECTED DTC No. DETECTED FAILURE CONDITION CHECK FOR ITEM Ignition Ignition switch signal is not input to the Ignition switch, lead wire/coupler, P1650 switch ECM. etc. HO2 sensor HO2 sensor output voltage is not input HO2 sensor circuit open or to ECM during engine operation and shorted to ground running condition. - Page 315 SERVICING INFORMATION 10-5 Complaint Symptom and possible causes Remedy Engine idles poorly. 1. Valve clearance out of adjustment Adjust. 2. Poor seating of valves Replace or repair. 3. Defective valve guides Replace. 4. Worn rocker arms or cam surfaces Replace. 5.
- Page 316 10-6 SERVICING INFORMATION Complaint Symptom and possible causes Remedy Noisy engine Excessive valve chatter 1. Too large valve clearance Adjust. 2. Weakened or broken valve springs Replace. 3. Worn rocker arm or cam surface Replace. 4. Worn and burnt camshaft journal Replace.
- Page 317 SERVICING INFORMATION 10-7 Complaint Symptom and possible causes Remedy Engine runs poorly Defective engine internal/electrical parts in high speed range. 1. Weakened valve springs Replace. 2. Worn camshaft Replace. 3. Valve timing out of adjustment Adjust. 4. Too narrow spark plug gap Adjust.
- Page 318 10-8 SERVICING INFORMATION Complaint Symptom and possible causes Remedy Engine lacks power. Defective engine internal/electrical parts 1. Loss of valve clearance Adjust. 2. Weakened valve springs Replace. 3. Valve timing out of adjustment Adjust. 4. Worn piston rings or cylinder Replace.
-
Page 319: Radiator (Cooling System)
SERVICING INFORMATION 10-9 Complaint Symptom and possible causes Remedy Engine overheats Defective engine internal parts 1. Heavy carbon deposit on piston crown Clean. 2. Not enough oil in the engine Add oil. 3. Defective oil pump or clogged oil circuit Replace or clean. -
Page 320: Chassis
10-10 SERVICING INFORMATION CHASSIS Complaint Symptom and possible causes Remedy Heavy steering 1. Overtightened steering stem nut Adjust. 2. Broken bearing in steering stem Replace. 3. Distorted steering stem Replace. 4. Not enough pressure in tires Adjust. Wobbly handlebars 1. Loss of balance between right and left front forks Replace. -
Page 321: Brakes
SERVICING INFORMATION 10-11 BRAKES Complaint Symptom and possible causes Remedy Insufficient brake 1. Leakage of brake fluid from hydraulic system Repair or replace. power 2. Worn pads or disc Replace. 3. Oil adhesion on friction surface of pads Clean disc and pads. 4. -
Page 322: Electrical
10-12 SERVICING INFORMATION ELECTRICAL Complaint Symptom and possible causes Remedy No sparking or poor 1. Defective ignition coil Replace. sparking 2. Defective spark plug Replace. 3. Defective CKP sensor Replace. 4. Defective ECM Replace. 5. Defective TO sensor Replace. 6. Open-circuited wiring connections Repair or replace. -
Page 323: Battery
SERVICING INFORMATION 10-13 BATTERY Complaint Symptom and possible causes Remedy "Sulfation", acidic 1. Cracked battery case Replace the battery. white powdery sub- 2. Battery has been left in a run-down condition for a Replace the battery. stance or spots on long time surface of cell plates... -
Page 324: Wiring Diagram
10-14 SERVICING INFORMATION WIRING DIAGRAM... -
Page 325: Wiring Harness, Cable And Hose Routing
SERVICING INFORMATION 10-15 WIRING HARNESS, CABLE AND HOSE ROUTING WIRING HARNESS ROUTING TO sensor Handlebar switch (RH & LH) Front brake hose Side-stand Turn signal Rear brake hose Ignition switch relay relay Throttle cables lead wire Clamp Clamp Wiring harness Throttle cable Clamp Horn... - Page 326 10-16 SERVICING INFORMATION Fuel pump Fuse box Side-stand switch Clamp Wiring harness Clamp Clamp Wiring harness Engine ground wire Starter motor Wiring harness Generator Wiring harness HO2 sensor Generator Starter motor Clamp Engine ground wire Clamp Battery + cap Battery Trunk light switch Battery + terminal...
-
Page 327: Cable Routing
SERVICING INFORMATION 10-17 CABLE ROUTING Clamp Clamp Cable guide Handlebar switch (R) Cable guide bolt Front brake hose Seat lock bolt Clamp Rear brake pipe Seat Seat lock cable lock Rear brake hose Handlebar switch (L) Throttle cable No.2 (returning cable) Throttle cable No.1 (pulling cable) Frame cover... -
Page 328: Cooling System Hose Routing
10-18 SERVICING INFORMATION COOLING SYSTEM HOSE ROUTING Radiator inlet hose Radiator White outlet hose mark Overflow hose Reservoir Radiator cap Overflow hose Radiator Thermostat cover White mark Radiator outlet hose Cooling fan switch Radiator inlet hose Clamp Radiator Water pump Water pump O-ring Radiator inlet hose... -
Page 329: Brake Hose Routing
SERVICING INFORMATION 10-19 BRAKE HOSE ROUTING Rear brake pipe Engage the brake Rear brake hose hose clamps Front brake hose Front brake hose Clamp Tighten the brake hose mounting Pass through the rear Brake hose bolt after touching the edge of hose brake hose into the joint sleeve to the stopper. -
Page 330: Engine Electrical Parts Harness Routing
10-20 SERVICING INFORMATION ENGINE ELECTRICAL PARTS HARNESS ROUTING Ignition coil High tension code Starter motor Starter motor Ground wire Starter motor lead wire Starter motor lead wire bolt Grommet CKP sensor Generator stator Pass the high tension code to the outside of *1 Bring the tip of spark plug cap to downward. -
Page 331: Ho2 Sensor Harness Routing
SERVICING INFORMATION 10-21 HO2 SENSOR HARNESS ROUTING Clamp HO2 sensor Clamp HO2 sensor 48 N . m (4.8 kgf-m) Pass the HO2 sensor lead wire between the frame and engine. Do not protrude the HO2 sensor lead wire from the frame. -
Page 332: Speedometer Cable Routing
10-22 SERVICING INFORMATION SPEEDOMETER CABLE ROUTING Pass through the speedometer cable into the 1 Speedometer cable guide. Tighten the front axle nut to the specified torque 2 Cable guide after touching the stopper of speedometer gear box to the stopper of front fork outer tube. 3 Speedometer cable... -
Page 333: Throttle Body Hose Routing
SERVICING INFORMATION 10-23 THROTTLE BODY HOSE ROUTING Fuel hose Fuel tank Upper Upper ECT sensor 18 N . m (1.8 kgf-m) Lower Lower Clamp A Clamp B Fuel hose Clamp Throttle body IAP sensor Face the tab of intake pipe insulator to forward, Align the arrow mark on fuel pump with the fuel when installing it. -
Page 334: Drain Hose Routing
10-24 SERVICING INFORMATION DRAIN HOSE ROUTING 1 Footboard 3 Drain hose 2 Radiator duct 4 Rear lower leg shield... -
Page 335: Seat Molding Installation
SERVICING INFORMATION 10-25 SEAT MOLDING INSTALLATION 120 mm Outside 1 End of seat molding 3 Trunk box 2 Seat molding... -
Page 336: Exterior Parts Set-Up
10-26 SERVICING INFORMATION EXTERIOR PARTS SET-UP Windscreen Lower meter panel Inner front box Front cover Front box Front leg shield Lower leg shield *1 To frame *3 To side leg shield *2 From footboard *4 To rear lower leg shield... - Page 337 SERVICING INFORMATION 10-27 Rear footboard Rear footboard Side leg shield Footboard Side leg shield Rear lower leg shield *1 To front box *3 From lower leg shield *2 To frame...
- Page 338 10-28 SERVICING INFORMATION Lower frame cover Center frame cover Rear combination light Rear fender Frame cover (RH) Front frame cover Upper trunk box Footboard Lower trunk box Frame cover (LH) *1 To frame *2 To footboard...
-
Page 339: Drive Belt Cooling Filter And Clutch Cover Gasket Installation
SERVICING INFORMATION 10-29 DRIVE BELT COOLING FILTER AND CLUTCH COVER GASKET INSTALLATION Clutch cover gasket Clutch cover Drive V-belt cooling duct Cover Drive V-belt cooling filter... -
Page 340: Front Box Cushion Installation
10-30 SERVICING INFORMATION FRONT BOX CUSHION INSTALLATION 1 Front box 3 Cushion 2 Adhint of cushion... -
Page 341: Side-Stand Installation
SERVICING INFORMATION 10-31 SIDE-STAND INSTALLATION ITEM N·m kgf-m CENTER STAND INSTALLATION... -
Page 342: Special Tools
10-32 SERVICING INFORMATION SPECIAL TOOLS 09900-20102 09900-20202 09900-20203 09900-06107 09900-06108 Vernier calipers Micrometer Micrometer Snap ring pliers Snap ring pliers (1/20 mm, 200 mm) (1/100 mm, 25 – 50 mm) (1/100 mm, 50 – 75 mm) 09900-20205 09900-20530 09900-20602 09900-20605 09900-20607 Micrometer Cylinder gauge set... - Page 343 SERVICING INFORMATION 10-33 09915-64512 Compression 09910-32812 09910-32840 09913-70210 gauge Crankshaft Crankshaft installer 09913-50121 Bearing installer 09915-63311 installer attachment Oil seal remover (Adaptor) 09915-70610 09915-74511 09915-74521 09915-77331 Oil pressure Oil pressure Oil pressure Oil pressure 09916-10911 gauge adaptor gauge gauge hose gauge Valve lapper set 09916-14910...
- Page 344 10-34 SERVICING INFORMATION 09920-13120 Crankcase/ 09921-20210 09921-20240 09922-21410 09922-31420 Crankshaft Bearing remover Bearing remover Long socket Clutch spring separator (12 mm) wrench (46 mm) compressor 09924-84521 09925-18011 09930-10121 09930-11910 09923-73210 Bearing installer Steering bearing Spark plug socket Torx wrench Bearing remover installer wrench set 09930-11930...
- Page 345 SERVICING INFORMATION 10-35 09940-40220 09940-30230 09940-40211 Fuel pressure Hexagon socket 09940-34520 09940-34531 Fuel pressure gauge hose (17 mm) T-handle Attachment (A) gauge adapter attachment 09940-51410 Steering bearing 09940-52861 09941-34513 09941-51012 09941-54911 installer attach- Front fork oil seal Steering outer Ring lock nut Bearing outer race ment installer set...
-
Page 346: Tightening Torque
10-36 SERVICING INFORMATION TIGHTENING TORQUE ENGINE ITEM N·m kgf-m Cylinder head cover bolt Initial Final Camshaft journal holder bolt Cylinder head bolt Initial Final Cylinder head nut 6 mm Cylinder nut 6 mm Rocker arm adjuster lock-nut Exhaust pipe nut Muffler mounting bolt Starter clutch bolt Crankshaft nut... -
Page 347: Fi System And Intake Air System
SERVICING INFORMATION 10-37 FI SYSTEM AND INTAKE AIR SYSTEM N·m kgf-m ITEM CKP sensor bolt HO2 sensor Fuel pump retainer TP sensor mounting screw 0.18 COOLING SYSTEM N·m kgf-m ITEM Cooling fan thermo-switch Engine coolant temperature gauge Water pump mounting bolt Cooling fan mounting bolt 0.84 ECT sensor... -
Page 348: Tightening Torque Chart
10-38 SERVICING INFORMATION TIGHTENING TORQUE CHART For other bolts and nuts listed previously, refer to this chart: Bolt diameter Conventional or "4" marked bolt "7" marked bolt A (mm) N·m kgf-m N·m kgf-m 0.15 0.23 0.45 0.55 13.5 10.5 21.0 16.0 24.0 Conventional bolt... -
Page 349: Service Data
SERVICING INFORMATION 10-39 SERVICE DATA VALVE + VALVE GUIDE Unit: mm ITEM STANDARD LIMIT Valve diam. 22.0 — 19.0 — Valve clearance (when cold) 0.05 – 0.10 — 0.17 – 0.22 — Valve guide to valve stem 0.010 – 0.037 —... - Page 350 10-40 SERVICING INFORMATION CYLINDER + PISTON + PISTON RING Unit: mm ITEM STANDARD LIMIT Compression pressure 1 500 kPa 1 650 kPa (16.5 kgf/cm²) (15.0 kgf/cm Piston to cylinder clearance 0.020 – 0.030 0.120 Cylinder bore No nicks or 57.000 – 57.015 scratches Piston diameter 56.975 –...
- Page 351 SERVICING INFORMATION 10-41 TRANSMISSION Unit: mm Except ratio ITEM SPECIFICATION NOTE Reduction ratio Variable change (2.829 – 0.744) — Final reduction ratio 9.166 (44/16 × 50/15) — Drive V-belt width 22.4 21.4 Movable driven face spring free 130.0 123.5 length INJECTOR + FUEL PUMP + FUEL PRESSURE REGULATOR ITEM SPECIFICATION...
- Page 352 10-42 SERVICING INFORMATION THERMOSTAT + RADIATOR + FAN + COOLANT ITEM STANDARD/SPECIFICATION LIMIT Thermostat valve opening temper- Approx. 82 °C — ature Thermostat valve lift Over 3 mm at 95 °C — Engine coolant temperature sensor 20 °C Approx. 2.45 kΩ —...
- Page 353 SERVICING INFORMATION 10-43 ELECTRICAL Unit: mm ITEM STANDARD/SPECIFICATION NOTE Spark plug NGK: CR8E Type DENSO: U24ESR-N 0.7 – 0.8 Spark performance Over 8.0 at 1 atm. 158 – 238 Ω CKP sensor resistance W – G + probe: W, CKP sensor peak voltage 2.0 V and more - probe: G 1.2 –...
- Page 354 10-44 SERVICING INFORMATION BRAKE + WHEEL Unit: mm ITEM STANDARD LIMIT Brake disc thickness Front 4.5 ± 0.2 Rear 4.5 ± 0.2 Brake disc runout — 0.30 Master cylinder bore Front 11.000 – 11.043 — Rear 14.000 – 14.043 — Master cylinder piston diameter Front 10.957 –...
- Page 355 SERVICING INFORMATION 10-45 FUEL + OIL ITEM SPECIFICATION NOTE Fuel type Gasoline used should be graded 91 octane or higher. An unleaded gasoline type is recom- mended. Fuel tank capacity 11.0 L Engine oil and final gear box oil SAE 10W-40, API SF/SG or SH/SJ with JASO MA type Engine oil capacity Oil change...
- Page 356 Prepared by October, 2006 Part No. 99500-31350-01E Printed in Japan...
- Page 357 Printed in Japan...
Posted by: ellaellahathawaye0270619.blogspot.com
Source: https://www.manualslib.com/manual/1053929/Suzuki-Burgman-Uh125.html
Post a Comment